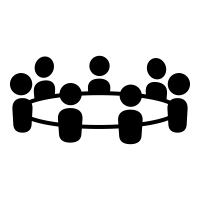
For those who want to progress in the field of construction management, accreditation is essential. Accreditation guarantees that a university or college's program meets the professional standards of the field it prepares graduates for. Learn more about the types of accreditation available, including ABET, ACCE, and Louisiana State University.
ABET accreditation provides assurance that a college or university program meets the quality standards of the profession for which it prepares graduates
The ABET accreditation process ensures that a college or university program meets quality standards and prepares its graduates to be successful in their chosen profession. ABET’s voluntary peer-review process, which is highly regarded globally, adds value in technical programs.
A voluntary accreditation process for ABET is carried out by a team that includes volunteers from government, industry, academia, and the private sector. The team's focus is on the program's faculty and institutional support.
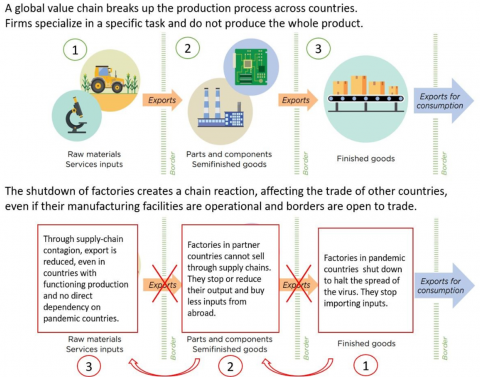
Accreditation by ACCE
ACCE accreditation for construction management programs is a valuable asset to prospective students, employers, and employees. Accredited programs give students the skills and knowledge needed to succeed in a career as a construction manager. Accreditation also makes it easier to find high-quality employees for employers. Accredited programs encourage faculty leadership development, foster network building, and keep current with the latest construction trends.
American Council for Construction Education accredits 2 levels of education in construction management. The Associate of Applied Science is accredited and the Bachelor of Science is accredited by the American Council for Construction Education. The Bachelor's program includes a capstone course, internships, and a minimum of three years. Both programs require a minimum GPA (3.5) and a minimum GRE score (550). In addition, applicants may be allowed to apply up to nine credits from another institution if they meet certain academic requirements. ACCE accreditation requires that accredited programs in construction management education maintain high standards. They must also align their educational programs to industry requirements.
ABET accreditation
Accreditation by ABET for construction management programs is a great way of ensuring quality education and to make sure that program content is reviewed by an independent governing body. Accreditation of construction management programs is usually granted by the Accreditation board for Engineering and Technological (ABET). The ABET accreditation process requires that programs adhere to certain standards. Accredited programs provide a foundation for students to be prepared for technical fields as well as keeping them current on emerging technologies.
Some schools have more than one curricula. In such cases, the curriculum may contain core courses common to both programs. This may lead to student competition and overextension of resources.
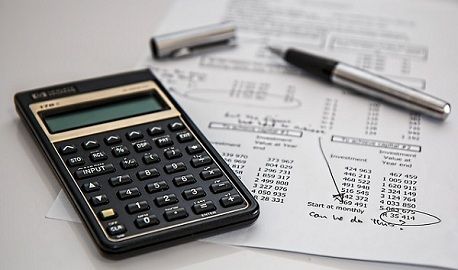
Louisiana State University accreditation
Louisiana State University offers a master's in construction management. This will equip you with the knowledge and skills to manage a construction project. This program will teach you about project planning, design, construction delivery, and more. Additionally, you will learn how to incorporate sustainable practices in the construction process. This program is approved by the American Council for Construction Education. The program includes leadership courses as well as core construction courses to help you become skilled construction managers.
Whether you're looking for a career in construction management, or are just interested in the field as a career change, Louisiana State University offers an online Bachelor of Science in Construction Management. The program consists six CM courses that will give you a foundational knowledge of the field. After completing the program requirements, the field will open up to you.
FAQ
How can a manager motivate his/her staff?
Motivation is the desire for success.
You can get motivated by doing something enjoyable.
You can also be motivated by the idea of making a difference to the success and growth of your organization.
For example: If you want to be a doctor, you might find it more motivating seeing patients than reading medical books all day.
Motivation comes from within.
Perhaps you have a strong sense to give back, for example.
Maybe you like working hard.
If you don’t feel motivated, find out why.
Then, consider ways you could improve your motivation.
What are the steps of the management decision-making process?
The decision-making process of managers is complicated and multifaceted. This involves many factors including analysis, strategy and planning, implementation, measurement and evaluation, feedback, feedback, and others.
It is important to remember that people are human beings, just like you. They make mistakes. As such, there are always opportunities for improvement, especially when you put in the effort to improve yourself.
This video shows you how management makes decisions. We discuss the different types of decisions and why they are important, every manager should know how to navigate them. These topics are covered in this course:
What role can a manager fill in a company’s management?
Each industry has a different role for a manager.
In general, a manager controls the day-to-day operations of a company.
He/she ensures the company meets its financial commitments and produces goods/services that customers demand.
He/she ensures employees adhere to all regulations and quality standards.
He/she plans new products and services and oversees marketing campaigns.
What are management concepts, you ask?
Management Concepts are the principles and practices managers use to manage people and resources. They cover topics such as job descriptions and performance evaluations, human resource policies, training programs, employee motivation, compens systems, organizational structure, among others.
What is Six Sigma and how can it help you?
It's a strategy for quality improvement that emphasizes customer care and continuous learning. This is an approach to quality improvement that uses statistical techniques to eliminate defects.
Motorola developed Six Sigma in 1986 to help improve its manufacturing processes.
This idea quickly spread throughout the industry. Today, many organizations use six sigma methods for product design, production and delivery.
Statistics
- The average salary for financial advisors in 2021 is around $60,000 per year, with the top 10% of the profession making more than $111,000 per year. (wgu.edu)
- This field is expected to grow about 7% by 2028, a bit faster than the national average for job growth. (wgu.edu)
- 100% of the courses are offered online, and no campus visits are required — a big time-saver for you. (online.uc.edu)
- UpCounsel accepts only the top 5 percent of lawyers on its site. (upcounsel.com)
- As of 2020, personal bankers or tellers make an average of $32,620 per year, according to the BLS. (wgu.edu)
External Links
How To
How can Lean Manufacturing be done?
Lean Manufacturing is a method to reduce waste and increase efficiency using structured methods. These processes were created by Toyota Motor Corporation, Japan in the 1980s. The goal was to produce quality products at lower cost. Lean manufacturing eliminates unnecessary steps and activities from a production process. It is made up of five elements: continuous improvement, continuous improvement, just in-time, continuous change, and 5S. Pull systems allow customers to get exactly what they want without having to do extra work. Continuous improvement refers to continuously improving existing processes. Just-in-time refers to when components and materials are delivered directly to the point where they are needed. Kaizen refers to continuous improvement. It is achieved through small changes that are made continuously. Five-S stands for sort. It is also the acronym for shine, standardize (standardize), and sustain. These five elements are combined to give you the best possible results.
The Lean Production System
Six key concepts make up the lean manufacturing system.
-
Flow - focuses on moving information and materials as close to customers as possible.
-
Value stream mapping - break down each stage of a process into discrete tasks and create a flowchart of the entire process;
-
Five S’s - Sorted, In Order. Shine. Standardize. And Sustain.
-
Kanban: Use visual signals such stickers, colored tape, or any other visual cues, to keep track your inventory.
-
Theory of Constraints - Identify bottlenecks in the process, and eliminate them using lean tools such kanban boards.
-
Just-in Time - Send components and material directly to the point-of-use;
-
Continuous improvement - incremental improvements are made to the process, not a complete overhaul.