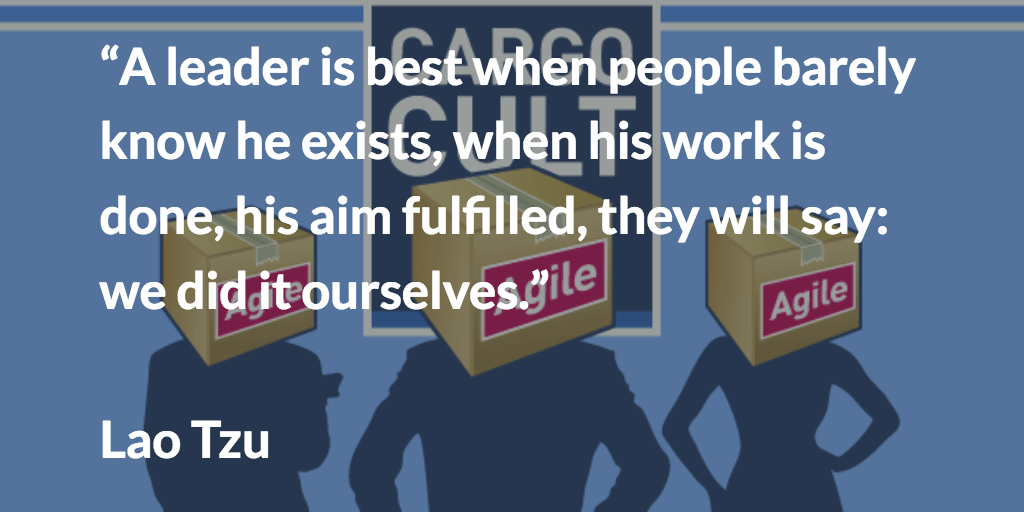
A cost benefit analysis is a great way to make the right business decision. This analysis assesses the cost of a new project to determine if it's worth the risk. The cost benefit analysis uses a combination of monetary and non-monetary metrics to determine the best course of action for your company. The most obvious benefit of this type of analysis is that it enables you to assess which projects are likely to be worthwhile investments.
The best way to conduct a cost benefit analysis is by using a project management software program. This software will help you collect all the information you need, and make sure you don’t forget any. It will display the results in an easy-to-understand format. You can either print or email reports. You can also get a 30-day free trial.
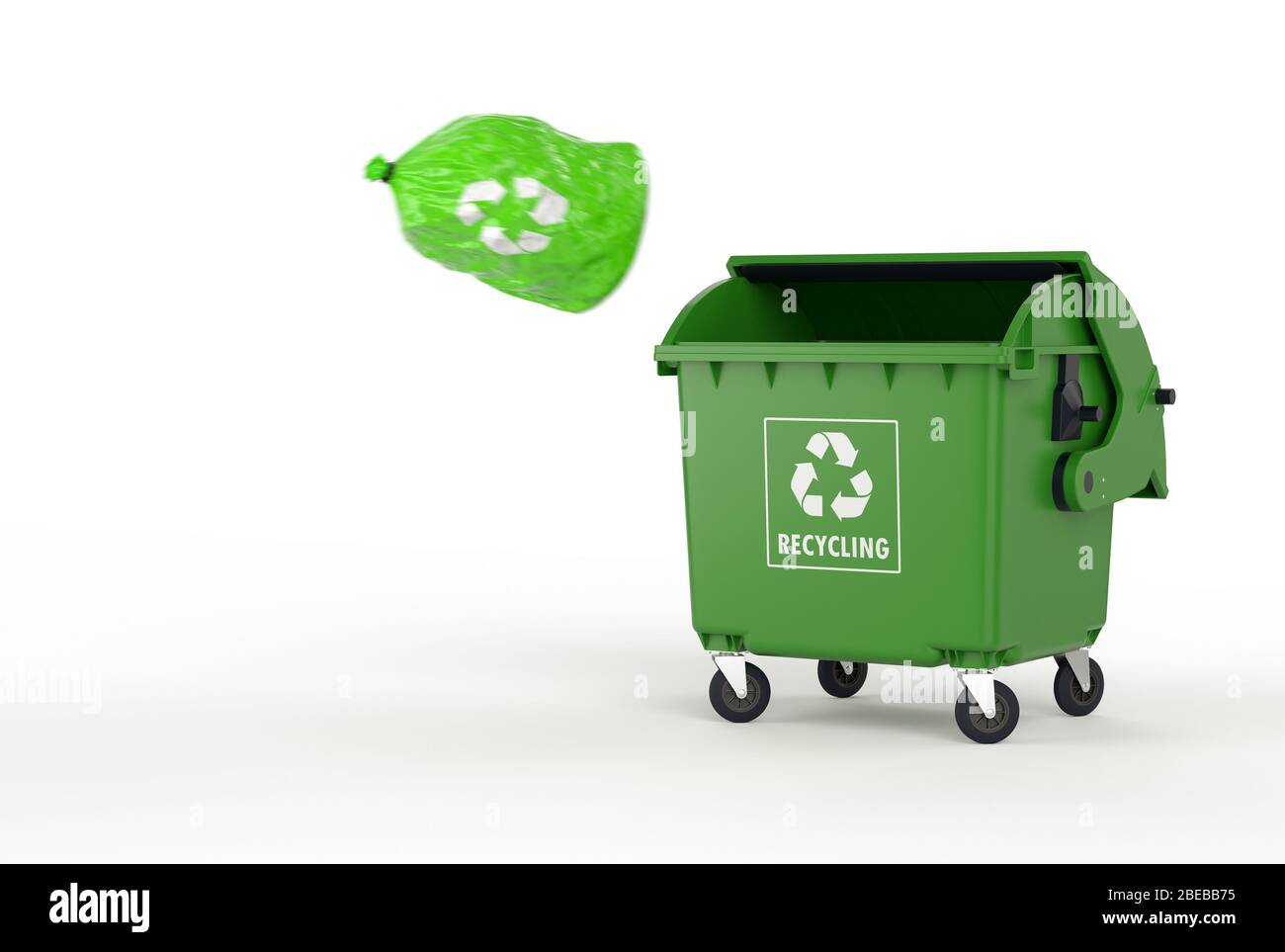
There are many options for project management software, but you should choose one that can accurately and informatively capture the cost of your project. For example, you may need to calculate the total number of people you need to complete a project. You may also want to calculate how many new equipment pieces you'll need. Unexpected costs should also be considered. This would include costs incurred throughout the project, such maintenance or training.
A dashboard with real-time information about your project status will be provided by the best software. Filtering data can be used to limit the information displayed. Even different reports can be created to suit different stakeholders.
Small to mid-sized projects are best suited for cost benefit analysis. This is not the best method to do a cost benefit analysis on large projects such as major renovations or new buildings. In addition to the obvious costs, you should also take into account opportunities that you may have missed. If you redesign a product, for example, you might have recouped some costs through additional profits.
A cost benefit analysis can also be a great way to assess whether or not a project is worthwhile. This will help you make informed decisions and avoid duplicating your efforts. A cost benefit analysis can help you compare projects and ensure that you don't waste your time on projects that won't make your business grow. This will save your time, energy, as well as money over the long-term.
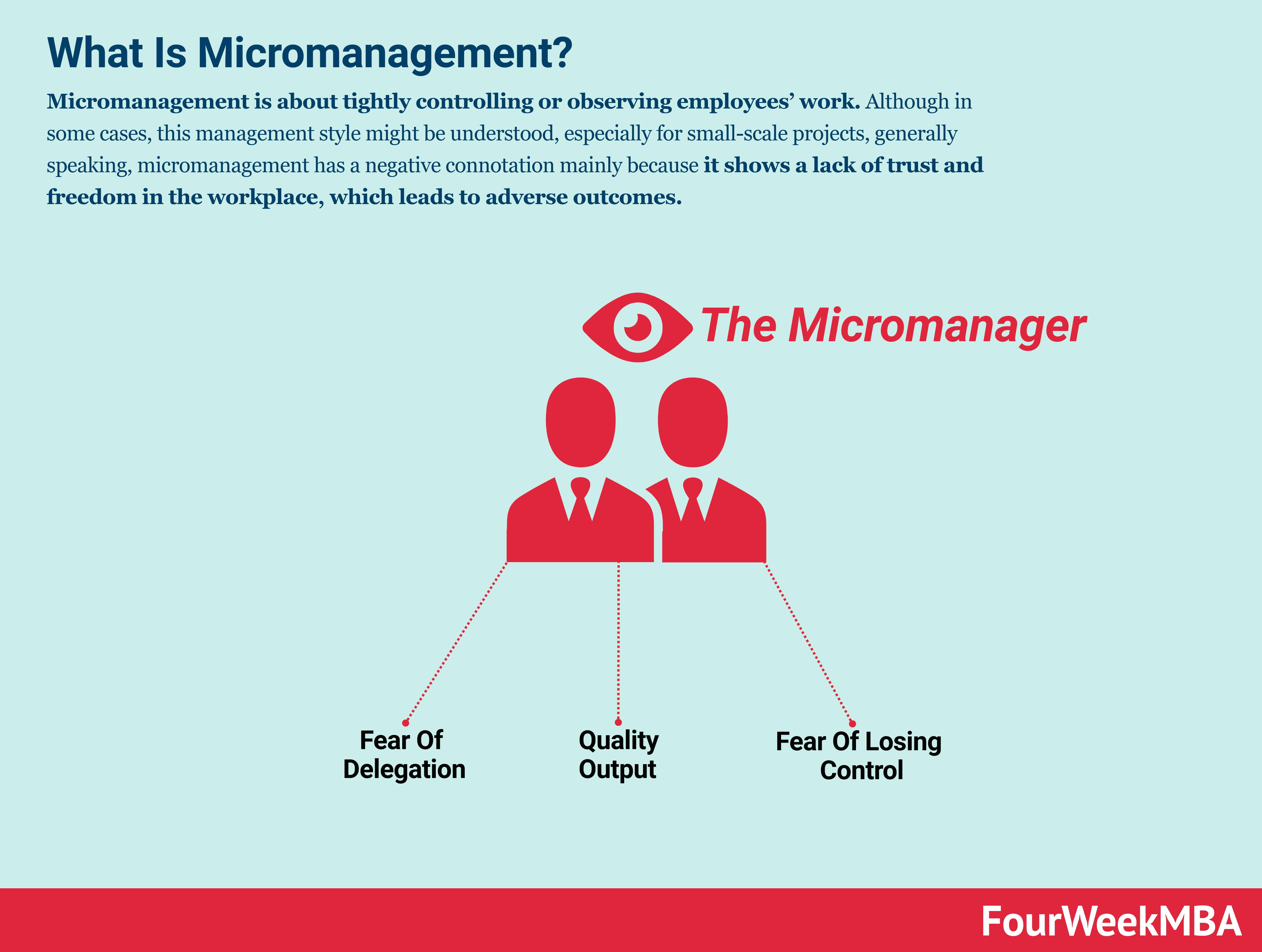
The software that you use to do the cost benefit analysis is just as important as its quality. For this type of analysis to be completed quickly, you will need robust project management software. You should also do a "sensitivity analysis" to assess the impact your project might have on you.
FAQ
It can sometimes seem difficult to make business decisions.
Complex systems with many moving parts are the hallmark of businesses. Their leaders must manage multiple priorities, as well as dealing with uncertainty.
Understanding how these factors impact the whole system is key to making informed decisions.
It is important to consider the functions and reasons for each part of the system. Next, consider how each piece interacts with the others.
You need to ask yourself if your previous actions have led you to make unfounded assumptions. If they don't, you may want to reconsider them.
If you're still stuck after all this, try asking someone else for help. They might have different perspectives than you, and could offer insight that could help you solve your problem.
What is Six Sigma?
It's an approach to quality improvement that emphasizes customer service and continuous learning. The goal is to eradicate defects through statistical techniques.
Six Sigma was developed at Motorola in 1986 as part of its efforts to improve manufacturing processes.
The idea quickly spread in the industry. Many organizations today use six-sigma methods to improve product design and production, delivery and customer service.
How can a manager enhance his/her leadership skills?
Good management skills are essential for success.
Managers must monitor the performance of subordinates constantly.
You must quickly take action if your subordinate fails to perform.
It is essential to know what areas need to be improved and how to do it.
Statistics
- The profession is expected to grow 7% by 2028, a bit faster than the national average. (wgu.edu)
- UpCounsel accepts only the top 5 percent of lawyers on its site. (upcounsel.com)
- Hire the top business lawyers and save up to 60% on legal fees (upcounsel.com)
- The average salary for financial advisors in 2021 is around $60,000 per year, with the top 10% of the profession making more than $111,000 per year. (wgu.edu)
- Your choice in Step 5 may very likely be the same or similar to the alternative you placed at the top of your list at the end of Step 4. (umassd.edu)
External Links
How To
How can you use the Kaizen method?
Kaizen means continuous improvement. This term was first used by Toyota Motor Corporation in the 1950s. It refers to the Japanese philosophy that emphasizes continuous improvement through small incremental changes. It's a process where people work together to improve their processes continuously.
Kaizen is one method that Lean Manufacturing uses to its greatest advantage. Kaizen is a concept where employees in charge of the production line are required to spot problems during the manufacturing process before they become major issues. This will increase the quality and decrease the cost of the products.
Kaizen is a way to raise awareness about what's happening around you. It is important to correct any problems immediately if they are discovered. It is important that employees report any problems they see while on the job to their managers.
Kaizen is based on a few principles. We always start from the end product and move toward the beginning. We can improve the factory by first fixing the machines that make it. We then fix the machines producing components, and the machines producing raw materials. We then fix the workers that work with those machines.
This approach is called 'kaizen' because it focuses on improving everything steps by step. After we're done with the factory, it's time to go back and fix the problem.
It is important to understand how to measure the effectiveness and implementation of kaizen in your company. There are many ways to tell if kaizen is effective. Another method is to see how many defects are found on the products. Another method is to determine how much productivity has improved since the implementation of kaizen.
Another way to know whether kaizen is working is to ask yourself why did you decide to implement kaizen. Was it just because it was the law or because you wanted to save money? Did you really believe it would lead to success?
Suppose you answered yes to any of these questions, congratulations! Now you're ready for kaizen.