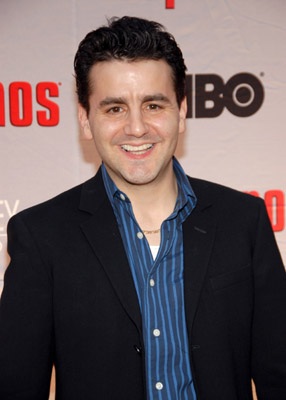
A common failure in managing risk is the lack of transparency. This was highlighted in the coronavirus deaths scandal. Other problems include the lack of data and siloed data. A lack of data and siloed data are also problems. Risk managers often settle for the data they have easy access to and fail to properly identify risks that could lead to negative consequences. This is a common problem and one that can be difficult to fix.
Negative risks
Managers can use five basic risk responses strategies to handle threats and negative outcomes. These strategies are dependent on the type and level of risk. They are dependent on the probability of occurrence as well as the impact that the risk will have. These strategies, which are the most effective, are used when risk is considered critical. If the risk is not so critical, then the transfer and acceptance strategy is recommended.
Positive and negative risks affect people, processes, technology, and resources. If managed properly, positive risks can lead to positive outcomes. Positive risks can lead to a project's ending sooner than expected or higher returns on investment. There are always negative risks. However, you can avoid them by using the best risk management practices. These risks are not without their challenges. They can have a negative impact on the project's timeline, budget, or schedule.
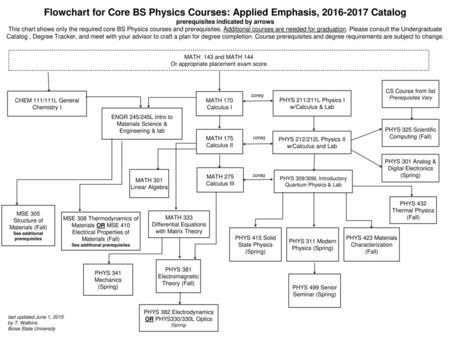
Communication
Risk management is all about communicating risks. Communication must be honest and open, no matter whether it is via a formal document. There is a risk that the risk will be misunderstood, but communication professionals can mitigate that risk by keeping it open and honest. Hurricane Harvey is a simple example of how to communicate risk. In 2017, Hurricane Harvey was a devastating hurricane that threatened Houston. Public officials used communication methods that included social media, national, as well as local media to warn affected residents to evacuate. Professionals must direct people to reliable sources for information.
Poor communication is one risk in project management. Poor communication is a major risk to the success or failure of a project. Communication can boost employee engagement as well as reduce miscommunications. A project's management risk assessment should include activities that improve communication efforts. Once it is done, project managers may take steps to mitigate the risk. This includes using a communication risk assessment tool and including stakeholders in the process.
Consultation
All stakeholders must be involved in the risk management process. You can have both external and internal partners involved, or even stakeholders not directly related to the project. So that all parties understand the risks and expectations, it is crucial to involve key stakeholders in the risk assessment process. Project teams must include all stakeholders in the risk assessment and management process to ensure that there is adequate consultation. These are some ways to ensure that all stakeholders are included in the consultation process.
In addition to assessing risks, a risk management consultant will help prioritize risks. This is important because high-risk risks require immediate attention while lower-risk ones will require a less drastic remediation plan. Consulting is a great way for organizations to identify risks and design a risk management program that meets their specific needs. Consulting can help organizations identify risks and develop an action plan. This will improve risk management.
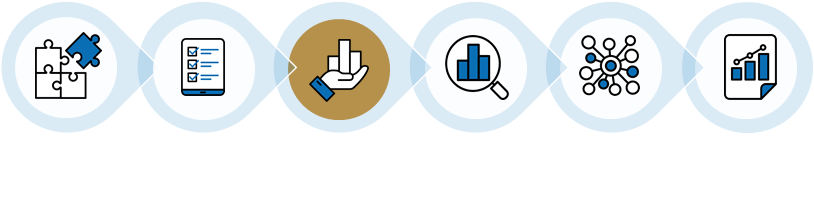
Top-down
Top-down risk management has its advantages and disadvantages. To set up, it takes time, effort and expert knowledge. Second, it tends to be bespoke - what one manager learned in one industry may not necessarily apply to another. Nevertheless, it has great potential as a risk management tool. Though not widely adopted, it is becoming more popular. Here are some other reasons why.
When a project is in its initial stages, top-down risks management techniques can be most useful. Risk management is most beneficial in the early stages of a project. This stage also allows for the application of the lessons learned from previous projects. Top-down risk analysis can also contribute to managerial accountability by incorporating evidenced-based top-down risks models and techniques from past projects. Top-down risk management techniques are a great way to reduce project risk if they are used correctly. They can also help teams and managers meet their financial obligations towards stakeholders.
FAQ
Why is it so important for companies that they use project management techniques
Project management techniques are used to ensure that projects run smoothly and meet deadlines.
This is because most businesses rely on project work for their products and services.
Companies need to manage these projects efficiently and effectively.
Companies can lose time, money, and reputation if they don't have a good project management system.
What is Six Sigma and how can it help you?
It is a way to improve quality that places emphasis on customer service and continuous learning. This is an approach to quality improvement that uses statistical techniques to eliminate defects.
Motorola's 1986 efforts to improve manufacturing process efficiency led to the creation of Six Sigma.
The idea quickly spread in the industry. Many organizations today use six-sigma methods to improve product design and production, delivery and customer service.
What are the 3 basic management styles?
There are three types of management: participative, laissez faire, and authoritarian. Each style is unique and has its strengths as well as weaknesses. Which style do YOU prefer? Why?
Autoritarian - The leader sets direction and expects everyone else to follow it. This style works best in large organizations that are stable and well-organized.
Laissez-faire – The leader gives each individual the freedom to make decisions for themselves. This style is best when the organization has a small but dynamic group.
Participative: The leader listens to everyone's ideas and suggestions. This style is best for small organizations where everyone feels valued.
Statistics
- This field is expected to grow about 7% by 2028, a bit faster than the national average for job growth. (wgu.edu)
- Hire the top business lawyers and save up to 60% on legal fees (upcounsel.com)
- The BLS says that financial services jobs like banking are expected to grow 4% by 2030, about as fast as the national average. (wgu.edu)
- As of 2020, personal bankers or tellers make an average of $32,620 per year, according to the BLS. (wgu.edu)
- Your choice in Step 5 may very likely be the same or similar to the alternative you placed at the top of your list at the end of Step 4. (umassd.edu)
External Links
How To
How can you implement the Kaizen technique?
Kaizen means continuous improvement. This Japanese term refers to the Japanese philosophy of continuous improvement that emphasizes incremental improvements and constant improvement. It's a team effort to continuously improve processes.
Kaizen is one of the most effective methods used in Lean Manufacturing. In this concept, employees who are responsible for the production line must identify problems that exist during the manufacturing process and try to solve them before they become big issues. This increases the quality of products and reduces the cost.
Kaizen is a way to raise awareness about what's happening around you. It is important to correct any problems immediately if they are discovered. It is important that employees report any problems they see while on the job to their managers.
When doing kaizen, there are some principles we must follow. Start with the end product, and then move to the beginning. In order to improve our factory's production, we must first fix the machines producing the final product. Next, we fix the machines which produce components. Finally, we repair the workers who are directly involved with these machines.
This is why it's called "kaizen" because it works step-by-step to improve everything. After we're done with the factory, it's time to go back and fix the problem.
You need to know how to measure the effectiveness of kaizen within your business. There are many ways to tell if kaizen is effective. One method is to inspect the finished products for defects. Another method is to determine how much productivity has improved since the implementation of kaizen.
Another way to know whether kaizen is working is to ask yourself why did you decide to implement kaizen. It was because of the law, or simply because you wanted to save some money. Did you really believe that it would be a success factor?
Congratulations if you answered "yes" to any of the questions. You are now ready to begin kaizen.