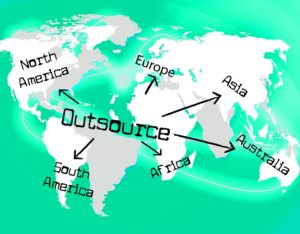
Risk Management is a process of reducing the possibility of loss or harm in an organization. This involves planning for potential negative outcomes and reducing the risk of profit-chasing and escalation. The process is crucial for the success of any organization. Risk management has many benefits. Here are some examples.
Reduces the likelihood of adverse events
Effective risk management begins with establishing a clear goal and a system to evaluate and reduce risks. It is challenging because it goes against many of the human biases. While rules and compliance may help reduce some risks, they are not sufficient to eliminate all. Management of risk must be proactive. This means managers need to consider risks holistically, establish processes that address them, and monitor and manage those risks.
Reduces the possibility of escalation
By establishing game plans for a range of situations that can lead to an escalation, risk management can significantly reduce the chance of escalation. While most risks have an uncertain end point, having a plan for every possible scenario can ensure that your organization is well prepared. This will help reduce the chances of escalation and minimize damage.
Reduces the likelihood of profit-chasing
Risk management is the topic of much discussion these days. Risk management means taking measures to reduce the risk of a loss. In order to avoid an increase in fuel costs, airlines might use financial derivatives. In order to protect their buildings from earthquakes, companies can raise their construction costs. Additionally, companies can join forces with others who face similar risk to reduce their cost.
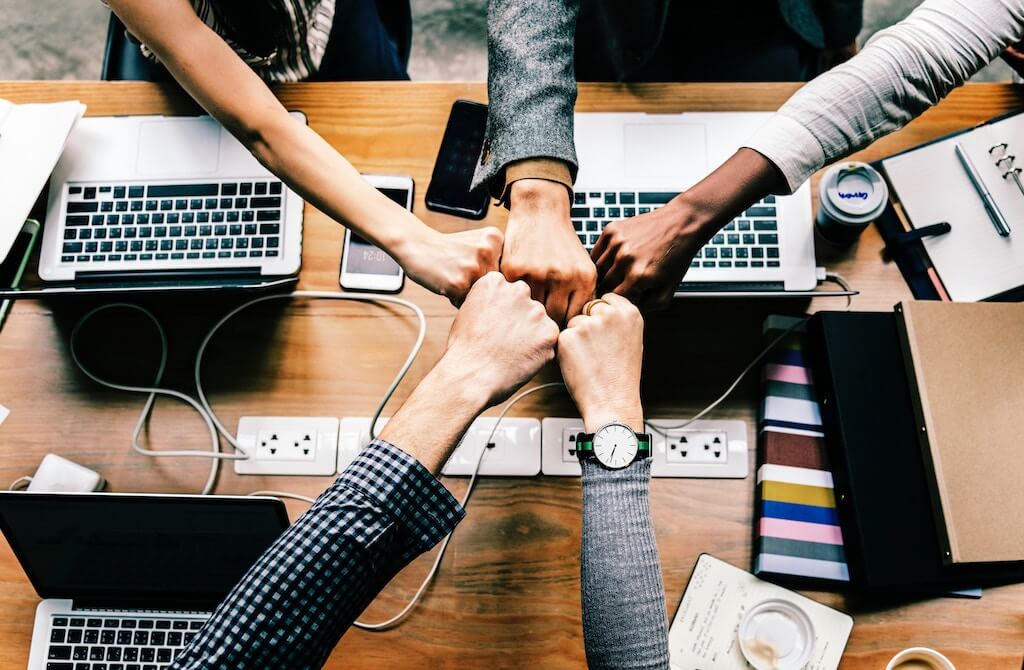
FAQ
What is a basic management tool that can be used for decision-making?
A decision matrix, a simple yet powerful tool for managers to make decisions, is the best. It helps them think systematically about all the options available to them.
A decision matrix is a way to organize alternatives into rows and columns. This allows you to easily see how each choice affects others.
In this example, we have four possible alternatives represented by the boxes on the left side of the matrix. Each box represents one option. The top row displays the current situation, and the bottom row shows what might happen if nothing is done.
The middle column shows the effect of choosing Option 1. This would result in an increase of sales of $2 million to $3million.
These are the results of selecting Options 2 or 3. These are positive changes - they increase sales by $1 million and $500 thousand respectively. These changes can also have negative effects. Option 2 increases costs by $100 thousand, while Option 3 decreases profits to $200 thousand.
The last column shows you the results of Option 4. This results in a decrease of sales by $1,000,000
The best thing about a decision matrix is the fact that you don't have to remember which numbers go with what. Simply look at the cells to instantly determine if one choice is better than the other.
The matrix already does all the work. It's as easy as comparing numbers in the appropriate cells.
Here's an example showing how you might use a Decision Matrix in your business.
You need to decide whether to invest in advertising. If you do, you'll be able to increase your revenue by $5 thousand per month. However, additional expenses of $10 000 per month will be incurred.
Look at the cell immediately below the one that states "Advertising" to calculate the net investment in advertising. It's $15,000. Advertising is a worthwhile investment because it has a higher return than the costs.
What is Six Sigma?
It's an approach to quality improvement that emphasizes customer service and continuous learning. It is a method that eliminates defects using statistical techniques.
Motorola created Six Sigma as part of their efforts to improve manufacturing processes in 1986.
The idea quickly spread in the industry. Many organizations today use six-sigma methods to improve product design and production, delivery and customer service.
What are the steps in the decision-making process in management?
The decision-making process for managers is complex and multifaceted. It involves many factors, such as analysis and strategy, planning, execution, measurement, evaluation, feedback etc.
When managing people, the most important thing to remember is that they are just human beings like you and make mistakes. You are always capable of improving yourself, and there's always room for improvement.
This video will explain how decision-making works in Management. We will explain the importance of different types decisions and how every manager can make them. Here are some topics you'll be learning about:
Statistics
- The average salary for financial advisors in 2021 is around $60,000 per year, with the top 10% of the profession making more than $111,000 per year. (wgu.edu)
- 100% of the courses are offered online, and no campus visits are required — a big time-saver for you. (online.uc.edu)
- This field is expected to grow about 7% by 2028, a bit faster than the national average for job growth. (wgu.edu)
- The BLS says that financial services jobs like banking are expected to grow 4% by 2030, about as fast as the national average. (wgu.edu)
- Our program is 100% engineered for your success. (online.uc.edu)
External Links
How To
How is Lean Manufacturing done?
Lean Manufacturing methods are used to reduce waste through structured processes. They were created by Toyota Motor Corporation in Japan in the 1980s. It was designed to produce high-quality products at lower prices while maintaining their quality. Lean manufacturing seeks to eliminate unnecessary steps and activities in the production process. It is composed of five fundamental elements: continuous improvement; pull systems, continuous improvements, just-in–time, kaizen, continuous change, and 5S. It is a system that produces only the product the customer requests without additional work. Continuous improvement is the continuous improvement of existing processes. Just-in-time is when components and other materials are delivered at their destination in a timely manner. Kaizen stands for continuous improvement. Kaizen can be described as a process of making small improvements continuously. Five-S stands for sort. It is also the acronym for shine, standardize (standardize), and sustain. These five elements are combined to give you the best possible results.
The Lean Production System
The lean production system is based on six key concepts:
-
Flow is about moving material and information as near as customers can.
-
Value stream mapping - Break down each stage in a process into distinct tasks and create an overview of the whole process.
-
Five S's: Sort, Shine Standardize, Sustain, Set In Order, Shine and Shine
-
Kanban – visual signals like colored tape, stickers or other visual cues are used to keep track inventory.
-
Theory of constraints: identify bottlenecks in your process and eliminate them using lean tools, such as kanban board.
-
Just-in-time delivery - Deliver components and materials right to your point of use.
-
Continuous improvement - make incremental improvements to the process rather than overhauling it all at once.