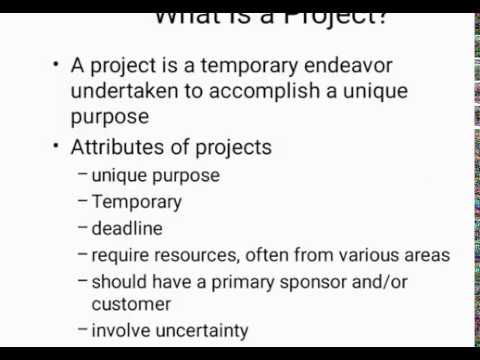
The Dynamics Supply Chain Management solution has comprehensive functionality for managing product lifecycles. This solution allows companies to create items for process or discrete manufacturing and test their quality. It can also match products with suppliers, submit RFQs, and evaluate suppliers. It also provides tools for managing inventories and inventory. It provides complete visibility of production and stock status. You can manage your order fulfillment from one location with this software.
Dynamics 365
Dynamics 365 Supply Chain Management is designed to increase the quality and operational efficiency of your end products. It integrates sales and purchasing processes, logistics, warehouse management, and warehouse administration. It provides intelligence into every transaction. Dynamics 365 SMCM helps you manage your distributed business and performs many other tasks such as asset and cost management, master planning and product information management.
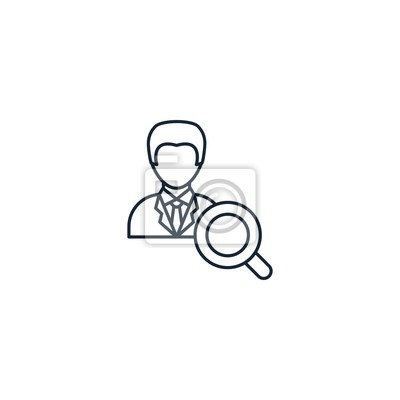
In addition, the solution has an advanced inventory management tool that automates the process for every step in the manufacturing process. This software allows you to optimize warehouse space, and streamline field service operations. Machine learning capabilities of the software allow it suggest better inventory control techniques. The software can help you achieve optimal inventory control and decrease downtime. This software helps you to efficiently manage the life cycle and productivity of finished goods, materials and employees.
Dynamics 365 Planning Optimization Add in
Microsoft Dynamics 365 can help you manage your supply chain. You might be interested in the planning optimization add on. This powerful tool can be used to help your company plan and manage inventory, transport, and warehouse functions. It can be used to analyze operations by using key performance indicators. It facilitates stock adjustment and capacity restrictions. It also allows for automated field service operations. Learn more about this powerful planning optimization program.
With the new add-in, master planning becomes even easier. You can now comply with multiple national standards for inventory accounting in a single system. This add-in also enables real-time inventory management, by gathering data simultaneously from multiple points of origin. In this rapidly-changing world, inventory visibility is essential for global supply chain efficiency. This add in allows you to focus your company's manufacturing efforts on the most important tasks.
Dynamics 365 Dynamics 365 Dynamics 365 Dynamics 365 Dynamics 365 Dynamics 365 Dynamics 365 Dynamics 365 Dynamics 365 Dynamics 365 Dynamics 365 Dynamics 365 Dynamics 365 Dynamics 365 Dynamics 365 Dynamics 365 Dynamics 365 Dynamics 365 Dynamics 365 Dynamics 365 Dynamics 365 Dynamics 365 Dynamics 365 Dynamics 365 Dynamics 365 Dynamics 365 Dynamics 365 Dynamics 365 Dynamics 365 Dynamics 365 Dynamics
Microsoft Dynamics is the latest version their business management software. It's the next generation in their supply chain management solutions. The cloud-based new solution integrates all the capabilities of Dynamics AX. It also helps you improve operational efficiency and improve the quality of your end product. It is possible to integrate existing systems with the software, allowing you to automate deliveries, inventory management, cost management, as well as cost management.
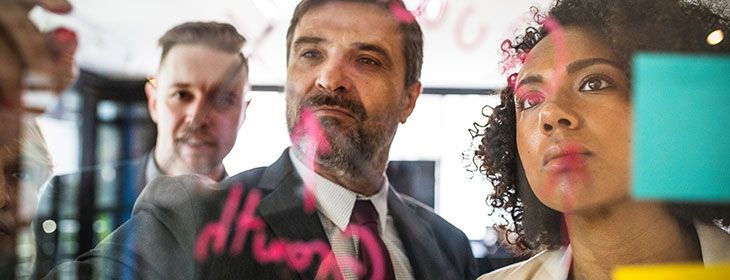
This solution integrates several functions of your supply chain into one, including inventory and purchasing. It provides real-time data to improve planning and decision-making. It supports accounting conservatism, as well as new reporting with Power BI. It comes with a step by step setup wizard that provides near-real time visibility into inventories. Additionally, it validates fulfillment dates via an ATP Check. It helps you allocate stocks based on demand and profitability, allowing you to make strategic decisions that benefit your business. It automates field service operations, which allows you to be up and running more quickly.
FAQ
What is TQM?
The industrial revolution saw the realization that prices alone were not sufficient to sustain manufacturing companies. This led to the birth of quality. To remain competitive, they had to improve quality as well as efficiency.
Management developed Total Quality Management to address the need for improvement. It focused on all aspects of an organisation's performance. It involved continuous improvement, employee participation, and customer satisfaction.
What are your main management skills
Managerial skills are crucial for every business owner, regardless of whether they run a small store in their locality or a large corporation. They are the ability to manage people and finances, space, money, and other factors.
You will need management skills to set goals and objectives, plan strategies, motivate employees, resolve problems, create policies and procedures, and manage change.
As you can see there is no end to the number of managerial tasks.
What does Six Sigma mean?
Six Sigma employs statistical analysis to identify problems, measure them and analyze root causes. Six Sigma also uses experience to correct problems.
The first step is to identify the problem.
Next, data are collected and analyzed in order to identify patterns and trends.
The problem is then rectified.
The data are then reanalyzed to see if the problem is solved.
This continues until the problem has been solved.
What are the main styles of management?
These are the three most common management styles: participative (authoritarian), laissez-faire (leavez-faire), and authoritarian. Each style has its advantages and disadvantages. Which style do YOU prefer? Why?
Autoritarian – The leader sets the direction for everyone and expects them to follow. This style is most effective when an organization is large, stable, and well-run.
Laissez-faire is a leader who allows everyone to make their own decisions. This style is best when the organization has a small but dynamic group.
Participative – Leaders are open to suggestions and ideas from everyone. This style is most effective in smaller organizations, where everyone feels valued.
What is the difference between TQM and Six Sigma?
The main difference in these two quality management tools lies in the fact that six sigma is focused on eliminating defects and total quality management (TQM), emphasizes improving processes and reducing costs.
Six Sigma is an approach for continuous improvement. This method emphasizes eliminating defects using statistical methods such p-charts, control charts, and Pareto analysis.
The goal of this method is to reduce variation in product output. This is achieved by identifying and addressing the root causes of problems.
Total quality management involves measuring and monitoring all aspects of the organization. It also includes training employees to improve performance.
It is frequently used as an approach to increasing productivity.
Why does it sometimes seem so hard to make good business decisions
Complex business systems have many moving parts. Their leaders must manage multiple priorities, as well as dealing with uncertainty.
It is important to understand the effects of these factors on the system in order to make informed decisions.
You need to be clear about the roles and responsibilities of each system. It is important to then consider how the individual pieces relate to each other.
Also, you should ask yourself if there have been any assumptions in your past behavior. If they don't, you may want to reconsider them.
If you're still stuck after all this, try asking someone else for help. They might see things differently than you and may have some insights that could help find a solution.
Statistics
- As of 2020, personal bankers or tellers make an average of $32,620 per year, according to the BLS. (wgu.edu)
- Your choice in Step 5 may very likely be the same or similar to the alternative you placed at the top of your list at the end of Step 4. (umassd.edu)
- This field is expected to grow about 7% by 2028, a bit faster than the national average for job growth. (wgu.edu)
- The profession is expected to grow 7% by 2028, a bit faster than the national average. (wgu.edu)
- Hire the top business lawyers and save up to 60% on legal fees (upcounsel.com)
External Links
How To
How can you implement Quality Management Plan (QMP).
QMP (Quality Management Plan) is a system to improve products and services by implementing continuous improvement. It focuses on the ability to measure, analyze and control processes and customer satisfaction.
QMP is a common method to ensure business performance. QMP's goal is to improve service delivery and production. A QMP should include all three aspects - Processes, Products, and Services. The QMP that only addresses one aspect of the process is called a Process QMP. The QMP that focuses on a Product/Service is called a "Product." QMP. If the QMP focuses on Customer Relationships, it's called a "Product" QMP.
Scope is the most important element in implementing a QMP. Strategy is the second. They are defined as follows:
Scope is what the QMP covers and how long it will last. For example, if you want to implement a QMP that lasts six months, then this scope will outline the activities done during the first six.
Strategy: This describes the steps taken to achieve the goals set out in the scope.
A typical QMP includes five phases: Design, Planning, Development and Implementation. The following describes each phase.
Planning: In this stage the QMP's objectives and priorities are established. Every stakeholder involved in the project is consulted to determine their expectations and needs. After identifying the objectives, priorities and stakeholder involvement, it's time to develop the strategy for achieving the goals.
Design: The design stage involves the development of vision, mission strategies, tactics, and strategies that will allow for successful implementation. These strategies can be implemented through the creation of detailed plans.
Development: This is where the development team works to build the capabilities and resources necessary for the successful implementation of the QMP.
Implementation involves the actual implementation using the planned strategies.
Maintenance: The maintenance of the QMP is an ongoing task.
Additionally, the QMP should include additional items:
Participation of Stakeholders: The QMP's success depends on the participation of stakeholders. They should be involved in planning, design, development and implementation of the QMP.
Project Initiation: The initiation of any project requires a clear understanding of the problem statement and the solution. The initiator must know the reason they are doing something and the expected outcome.
Time frame: It is crucial to know the time frame for the QMP. The simplest version can be used if the QMP is only being implemented for a short time. If you're looking to implement the QMP over a longer period of time, you may need more detailed versions.
Cost Estimation is another important aspect of the QMP. You cannot plan without knowing how much money you will spend. It is therefore important to calculate the cost before you start the QMP.
QMPs are more than just documents. They can also be updated as needed. It changes with the company. It should be reviewed on a regular basis to ensure that it is still meeting the company's needs.