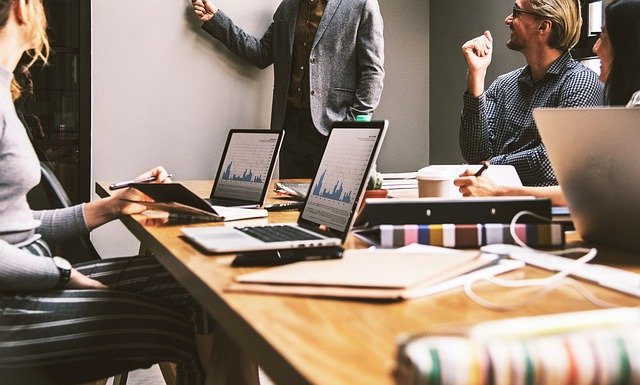
Management and business owners need to understand the importance of the supply chains in creating strategic value. It plays a vital role in customer satisfaction, brand image and profitability. If you understand the importance of the supply chain in creating value, it can become a strategic asset. Here's how to maximize its value:
Impact of e-commerce on supply chain efficiency
The supply chain has seen many changes due to the rapid rise of e-commerce. With customers increasingly expecting faster deliveries, warehouses need to adapt to changing business practices to keep up with demand. In the UK, 92% of households now shop online and parcel delivery is increasing globally. These changes have impacted the efficiency of the supply chain, which has had to deal with increased production and delivery volumes. The transformation occurring in the supply chain is expected to last for years.
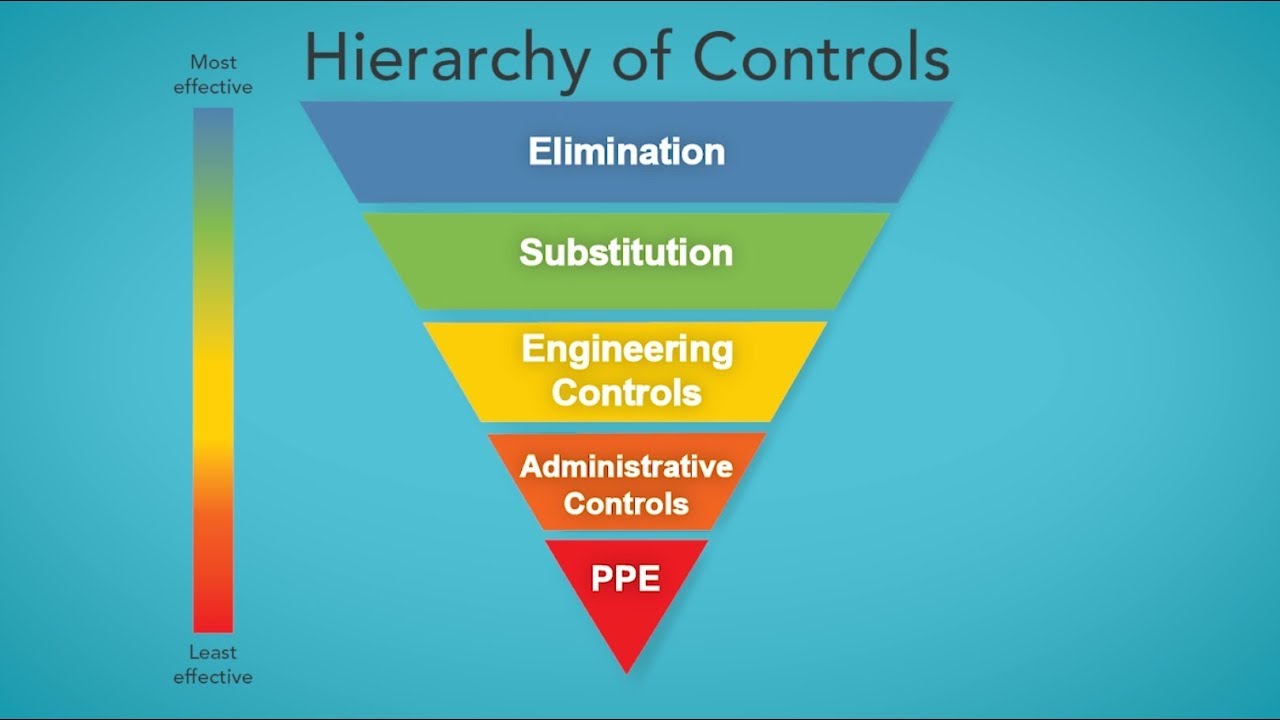
E-commerce, for instance, makes it easier for companies that they can exchange information with suppliers or customers. This eliminates the need for paper and other manual processes. It can also reduce transport costs as companies can combine shipments and use shipping agents that offer bulk discounts. E-commerce allows transport companies to upload documents online during the fulfillment process. This can help improve the efficiency of supply chains.
Customer perception of value and the impact of e-commerce
The ecommerce revolution changed how people shop as well as how companies operate. Retailers initially struggled to keep pace with changing consumer demands. As the industry developed and ecommerce gained popularity, retailers made rapid changes to meet consumers' needs. In the last decade, retailers focused on simplifying their processes to provide conveniences for customers. Consumers have become more sophisticated with technology such as cybersecurity, curbside pickup, and other innovations.
E-commerce is changing the way that consumers purchase and return products. A mobile device can be used to buy products or an estore kiosk. They don't need to wait for delivery or pay shipping costs. Moreover, consumers now expect free returns and buy more than they need. That means that the supply chain has to adjust to these new trends. E-commerce may also have an effect on supply chain productivity and inflation. Increasing competition can lower costs and drive inflation down.
Impact of digitalization on supply chain efficiency
Digitization has a major impact on supply chain efficiency. Digital technologies can improve supply chain speed and cash flow. Particularly, digital supply chains solutions can connect disparate systems to allow for faster communication within the organization. Digital supply chain solutions enable companies to make better decisions quicker and reduce the risk associated with supply chain disruptions. These solutions make full use of the data available.
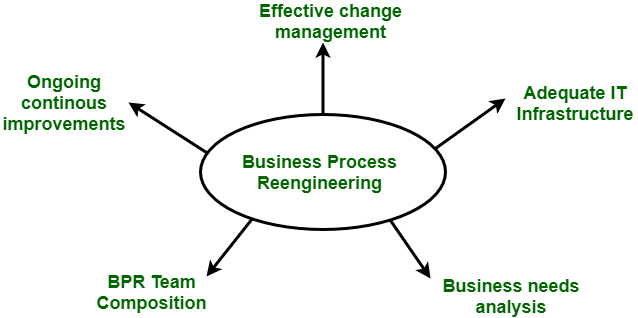
Supply chain leaders will need more real-time data to optimize their processes and make better strategic decisions. With access to real-time data, supply chain leaders will be able to better predict disruptions in the supply chain and improve visibility throughout the entire chain. AI-powered analytical tools can also improve planning processes. This will allow companies to get actionable insights, which can help them avoid out of stock situations and adjust their inventories. The benefits of digitizing supply chains will also be seen in the ability to reduce lead times and lower costs.
FAQ
What is Six Sigma?
Six Sigma uses statistical analysis to find problems, measure them, analyze root causes, correct problems, and learn from experience.
The first step in solving a problem is to identify it.
Next, data are collected and analyzed in order to identify patterns and trends.
Next, corrective steps are taken to fix the problem.
Finally, data is reanalyzed to determine whether the problem has been eliminated.
This cycle continues until the problem is solved.
What are some common mistakes managers make?
Sometimes managers make their job harder than they need to.
They may not delegate enough responsibilities to staff and fail to give them adequate support.
Many managers lack the communication skills to motivate and lead their employees.
Some managers create unrealistic expectations for their teams.
Managers may attempt to solve all problems themselves, rather than delegating it to others.
What kind people use Six Sigma?
Six Sigma will most likely be familiar to people who have worked in statistics and operations research. However, anyone involved in any aspect of business can benefit from using it.
It requires high levels of commitment and leadership skills to be successful.
How can we create a successful company culture?
A culture of respect and value within a company is key to a productive culture.
It is based on three principles:
-
Everyone has something to contribute
-
People are treated fairly
-
People and groups should respect each other.
These values are reflected by the way people behave. For example, they will treat others with courtesy and consideration.
They will listen to other people's opinions respectfully.
These people will inspire others to share thoughts and feelings.
A company culture encourages collaboration and communication.
People feel safe to voice their opinions without fear of reprisal.
They are aware that mistakes can be accepted if they are treated honestly.
The company culture promotes honesty, integrity, and fairness.
Everyone knows that they must always tell truth.
Everyone understands that there are rules and regulations which apply to them.
And no one expects special treatment or favors.
What's the difference between leadership & management?
Leadership is about being a leader. Management is about controlling others.
A leader inspires his followers while a manager directs the workers.
A leader motivates people and keeps them on task.
A leader develops people; a manager manages people.
What are management theories?
Management Concepts are the principles and practices managers use to manage people and resources. They include such topics as human resource policies, job descriptions, performance evaluations, training programs, employee motivation, compensation systems, organizational structure, and many others.
What is the difference between Six Sigma Six Sigma and TQM?
The key difference between the two quality management tools is that while six-sigma focuses its efforts on eliminating defects, total quality management (TQM), focuses more on improving processes and reducing cost.
Six Sigma is a methodology for continuous improvement. This approach emphasizes eliminating defects through statistical methods like control charts, Pareto analysis, and p-charts.
This method seeks to decrease variation in product output. This is accomplished by identifying the root cause of problems and fixing them.
Total quality management refers to the monitoring and measurement of all aspects in an organization. It also includes the training of employees to improve performance.
It is commonly used as a strategy for increasing productivity.
Statistics
- As of 2020, personal bankers or tellers make an average of $32,620 per year, according to the BLS. (wgu.edu)
- Hire the top business lawyers and save up to 60% on legal fees (upcounsel.com)
- Our program is 100% engineered for your success. (online.uc.edu)
- The profession is expected to grow 7% by 2028, a bit faster than the national average. (wgu.edu)
- 100% of the courses are offered online, and no campus visits are required — a big time-saver for you. (online.uc.edu)
External Links
How To
How do you apply the Kaizen method to your life?
Kaizen means continuous improvement. The term was coined in the 1950s at Toyota Motor Corporation and refers to the Japanese philosophy emphasizing constant improvement through small incremental changes. It's a team effort to continuously improve processes.
Kaizen, a Lean Manufacturing method, is one of its most powerful. Employees responsible for the production line should identify potential problems in the manufacturing process and work together to resolve them. This increases the quality of products and reduces the cost.
Kaizen is a way to raise awareness about what's happening around you. It is important to correct any problems immediately if they are discovered. So, if someone notices a problem while working, he/she should report it to his/her manager.
When doing kaizen, there are some principles we must follow. The end product is always our starting point and we work toward the beginning. If we want to improve our factory for example, we start by fixing the machines that make the final product. Next, we repair the machines that make components. Then, the machines that make raw materials. We then fix the workers that work with those machines.
This method is known as kaizen because it focuses upon improving every aspect of the process step by step. After we're done with the factory, it's time to go back and fix the problem.
To implement kaizen in your business, you need to find out how to measure its effectiveness. There are many methods to assess if kaizen works well. One method is to inspect the finished products for defects. Another method is to determine how much productivity has improved since the implementation of kaizen.
To determine if kaizen is effective, you should ask yourself why you chose to implement kaizen. You were trying to save money or obey the law? You really believed it would make you successful?
Congratulations if you answered "yes" to any of the questions. You're now ready to get started with kaizen.