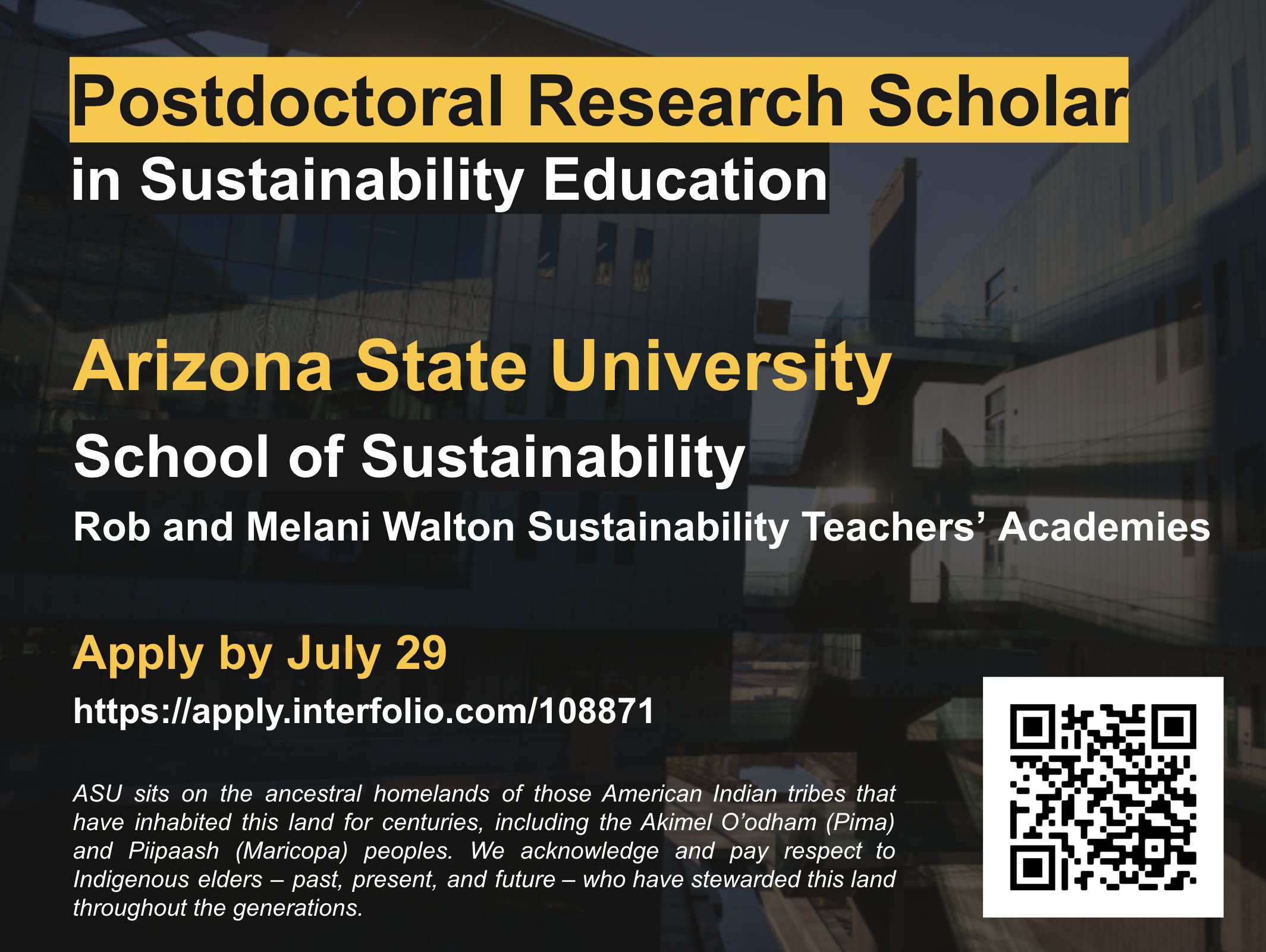
Waste management in Orlando: What are your responsibilities?
A waste management business is responsible to provide many services related the management and treatment. This includes municipal and private waste collection. These companies come up with innovative solutions for waste management that are compliant and environmentally friendly. These companies offer waste collection, recycling and disposal services. They are also experts in bulk liquid and bulk solids management.
The proper handling of hazardous or contaminated wastes is also a responsibility of professionals in waste management. They make sure that hazardous and contaminated materials are properly removed, while also complying with local regulations. Many waste professionals are also involved in ensuring that waste facilities work efficiently and that staff perform to their best.
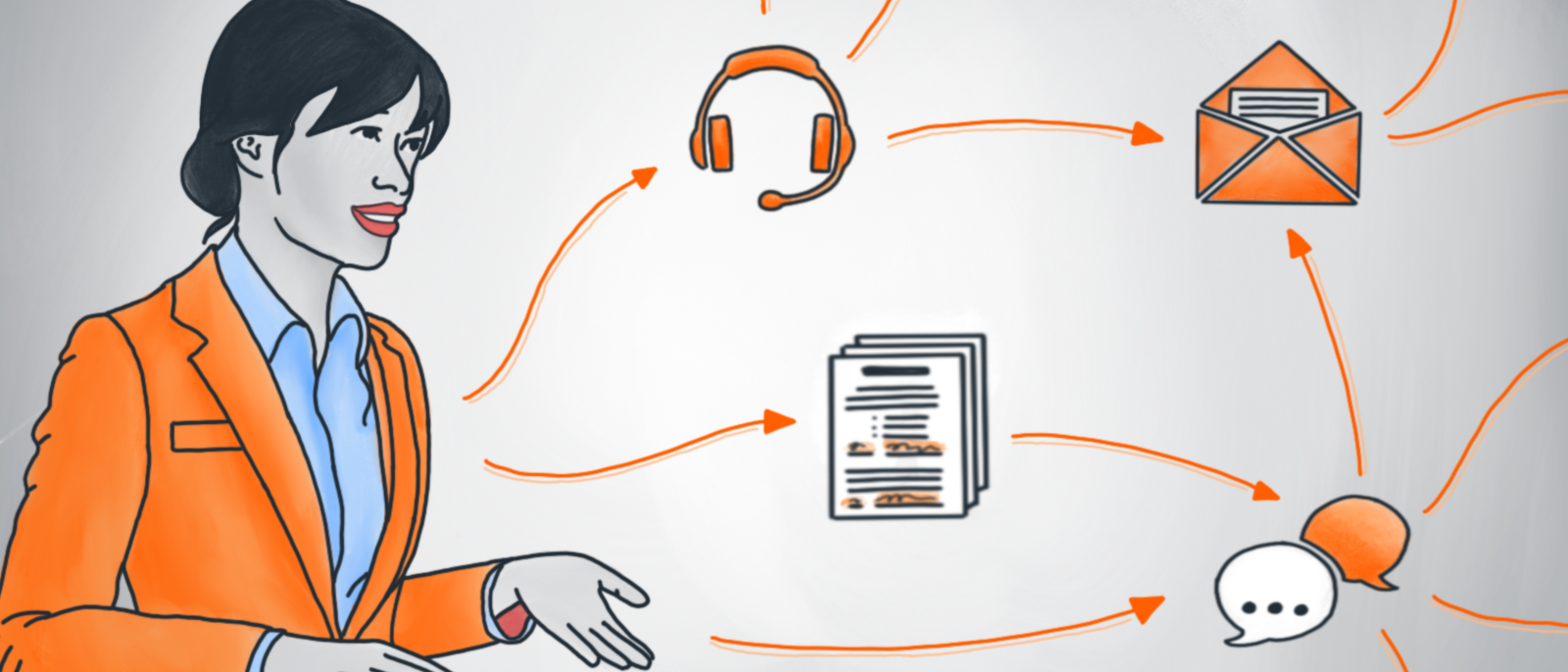
Salaries at a waste management company located in Orlando
You may be wondering how much money it would cost to get into waste management in Orlando. This job pays well in Orlando, FL. The salary of a waste management supervisor is usually $46,000. That's about 5% below the national average and over 25% below other metro salaries.
Although the salary information for this type job is subject to change depending on where you live, it is an average salary of $28,905. It is possible to expect a high income because of the competitive nature of Orlando's job market. The total compensation package includes paid vacations, holidays and personal days.
Companies that offer waste services in Orlando
Companies that offer waste management services in Orlando are able to help. Medical waste management is an integral part of any facility's waste management plan. UMI offers medical waste management in Orlando as well as the surrounding Kissimmee. They offer a wide range of sharps containers, as well other waste containment options for healthcare facilities. Their services include inventory management and sharps collection container storage containers.
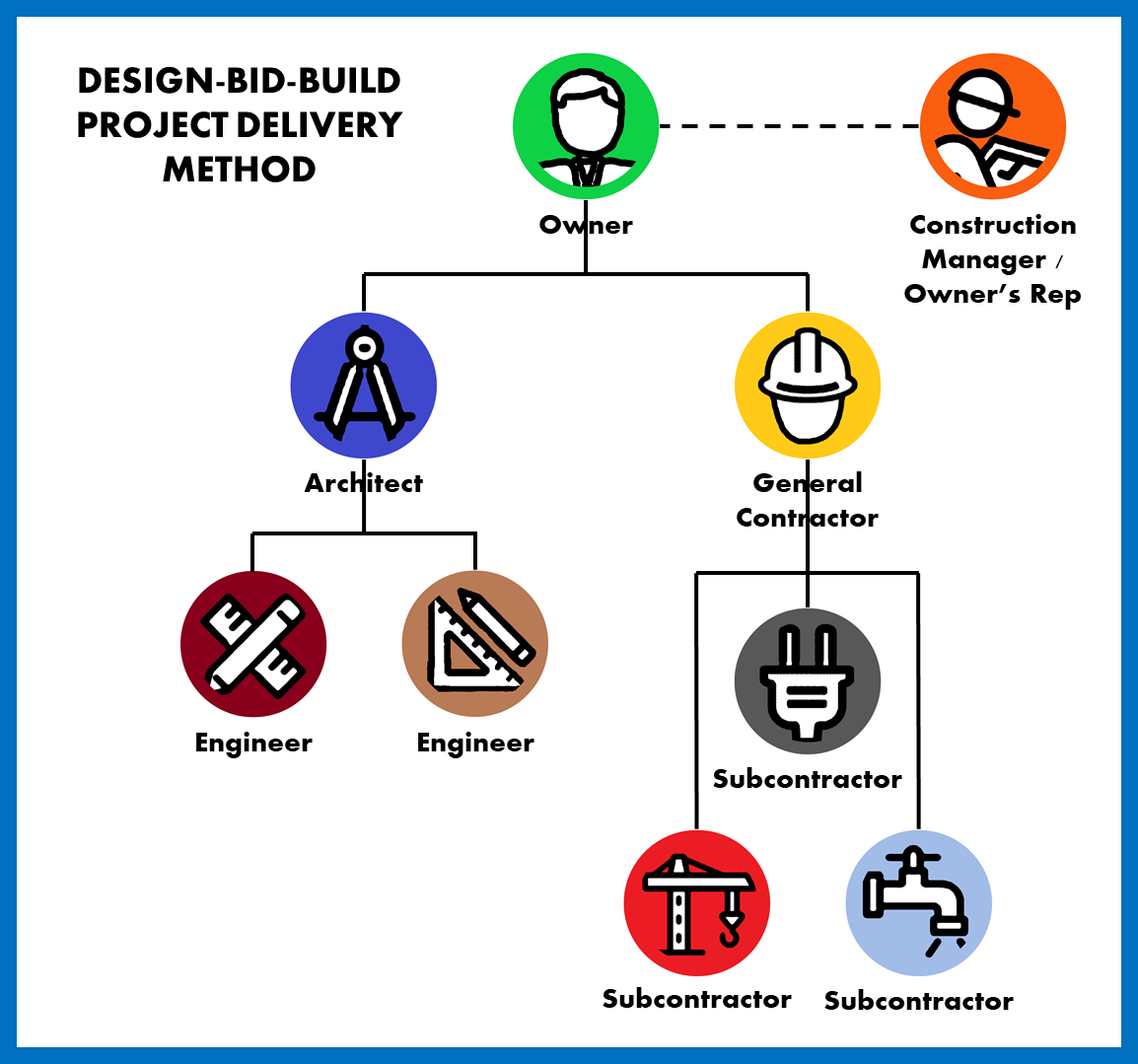
The Sunshine Recycling company offers waste management services throughout central Florida. Wawa Inc., an American convenience store/gas station combination franchise, has partnered with the Sunshine Recycling company. Wawa started out in New England and expanded along the east coast to include Florida. Wawa is well-known because of its fast food and fresh prepared foods.
FAQ
What is the difference between management and leadership?
Leadership is about influencing others. Management is all about controlling others.
Leaders inspire others, managers direct them.
A leader inspires others to succeed, while a manager helps workers stay on task.
A leader develops people; a manager manages people.
What is the role of a manager in a company?
There are many roles that a manager can play in different industries.
A manager generally manages the day to-day operations in a company.
He/she is responsible for ensuring that the company meets all its financial obligations and produces the goods or services customers want.
He/she will ensure that employees follow all rules and regulations, and adhere to quality standards.
He/she plans and oversees marketing campaigns.
How can a manager motivate employees?
Motivation is the desire to do well.
Enjoyable activities can motivate you.
You can also feel motivated by making a positive contribution to the success in the organization.
For example: If you want to be a doctor, you might find it more motivating seeing patients than reading medical books all day.
The inner motivation is another type.
For example, you might have a strong sense of responsibility to help others.
Or you might enjoy working hard.
If you don’t feel motivated, find out why.
Then think about how you can make your life more motivating.
How do you manage your employees effectively?
The key to effective management of employees is ensuring their happiness and productivity.
This includes setting clear expectations for their behavior and tracking their performance.
To do this successfully, managers need to set clear goals for themselves and for their teams.
They need to communicate clearly with staff members. They must communicate clearly with staff members.
They should also keep records of all activities within their team. These include:
-
What did we accomplish?
-
How much work was done?
-
Who did it, anyway?
-
How did it get done?
-
Why was this done?
This information can help you monitor your performance and to evaluate your results.
What is the difference in Six Sigma and TQM?
The main difference between these two quality-management tools is that six-sigma concentrates on eliminating defects while total QM (TQM), focuses upon improving processes and reducing expenses.
Six Sigma can be described as a strategy for continuous improvement. It emphasizes the elimination and improvement of defects using statistical methods, such as control charts, P-charts and Pareto analysis.
This method aims to reduce variation in product production. This is accomplished by identifying the root cause of problems and fixing them.
Total quality management refers to the monitoring and measurement of all aspects in an organization. It also includes the training of employees to improve performance.
It is often used as a strategy to increase productivity.
Six Sigma is so well-known.
Six Sigma is easy and can deliver significant results. It provides a framework that allows for improvement and helps companies concentrate on what really matters.
Statistics
- 100% of the courses are offered online, and no campus visits are required — a big time-saver for you. (online.uc.edu)
- Our program is 100% engineered for your success. (online.uc.edu)
- Your choice in Step 5 may very likely be the same or similar to the alternative you placed at the top of your list at the end of Step 4. (umassd.edu)
- The BLS says that financial services jobs like banking are expected to grow 4% by 2030, about as fast as the national average. (wgu.edu)
- UpCounsel accepts only the top 5 percent of lawyers on its site. (upcounsel.com)
External Links
How To
How do you do the Kaizen method?
Kaizen means continuous improvement. The term was coined in the 1950s at Toyota Motor Corporation and refers to the Japanese philosophy emphasizing constant improvement through small incremental changes. It is a process where people come together to improve their processes.
Kaizen is one the most important methods of Lean Manufacturing. Employees responsible for the production line should identify potential problems in the manufacturing process and work together to resolve them. This way, the quality of products increases, and the cost decreases.
Kaizen is an approach to making every worker aware and alert to what is happening around them. It is important to correct any problems immediately if they are discovered. It is important that employees report any problems they see while on the job to their managers.
Kaizen follows a set of principles. Start with the end product, and then move to the beginning. To improve our factory, for example, we need to fix the machines that produce the final product. We then fix the machines producing components, and the machines producing raw materials. We then fix the workers that work with those machines.
This is why it's called "kaizen" because it works step-by-step to improve everything. Once the factory is fixed, we return to the original site and work our way back until we get there.
It is important to understand how to measure the effectiveness and implementation of kaizen in your company. There are many methods to assess if kaizen works well. Another method is to see how many defects are found on the products. Another method is to determine how much productivity has improved since the implementation of kaizen.
Another way to know whether kaizen is working is to ask yourself why did you decide to implement kaizen. Is it because the law required it or because you want to save money. Did you really believe it would lead to success?
Congratulations! You are now ready to begin kaizen.