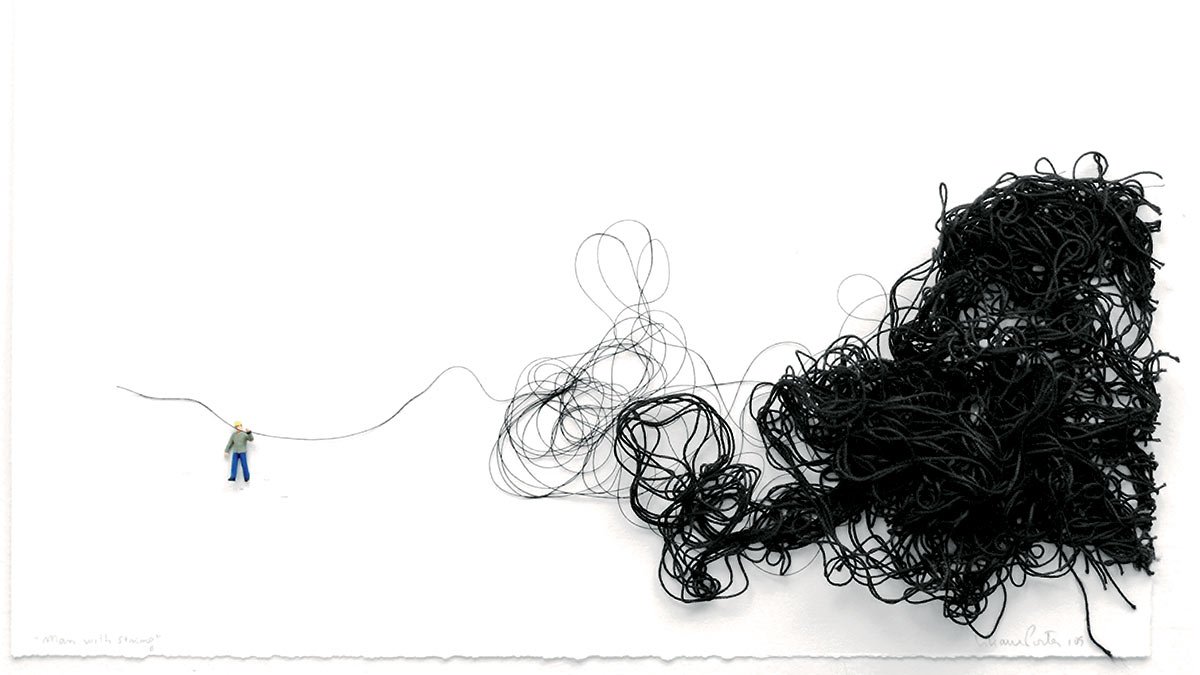
Logistics can be used to refer to many technical and complex operations. Logistics is usually used in military contexts. But it can also be used for any type of effort that needs prior planning. For example, it can describe a warehouse management system, document flow, or track and trace.
Supply chain
Logistics is the management and control of goods moving from their point-of-origin to their final destination. This serves customers and corporations. Logistics can be described as the organization and implementation complex operations. Logistics is essential for any business because it helps companies keep costs down and ensures timely deliveries.
Logistics involves the acquisition of raw material, transportation, warehousing/storage, documentation, and distribution. These activities make up the bulk of a company's overall cost but they are vital for satisfying customer requirements.
Warehouse management system
Warehouse management software (WMS) helps companies manage inventory, warehouse space and other logistics aspects. The right system can help you optimize inventory allocation, reduce costs, increase employee satisfaction, and improve productivity. WMS solutions are flexible and have features that can help you optimize and control your workflows. WMS systems usually include bin slotting. This maximizes storage space, while accounting for seasonal variation in inventory.
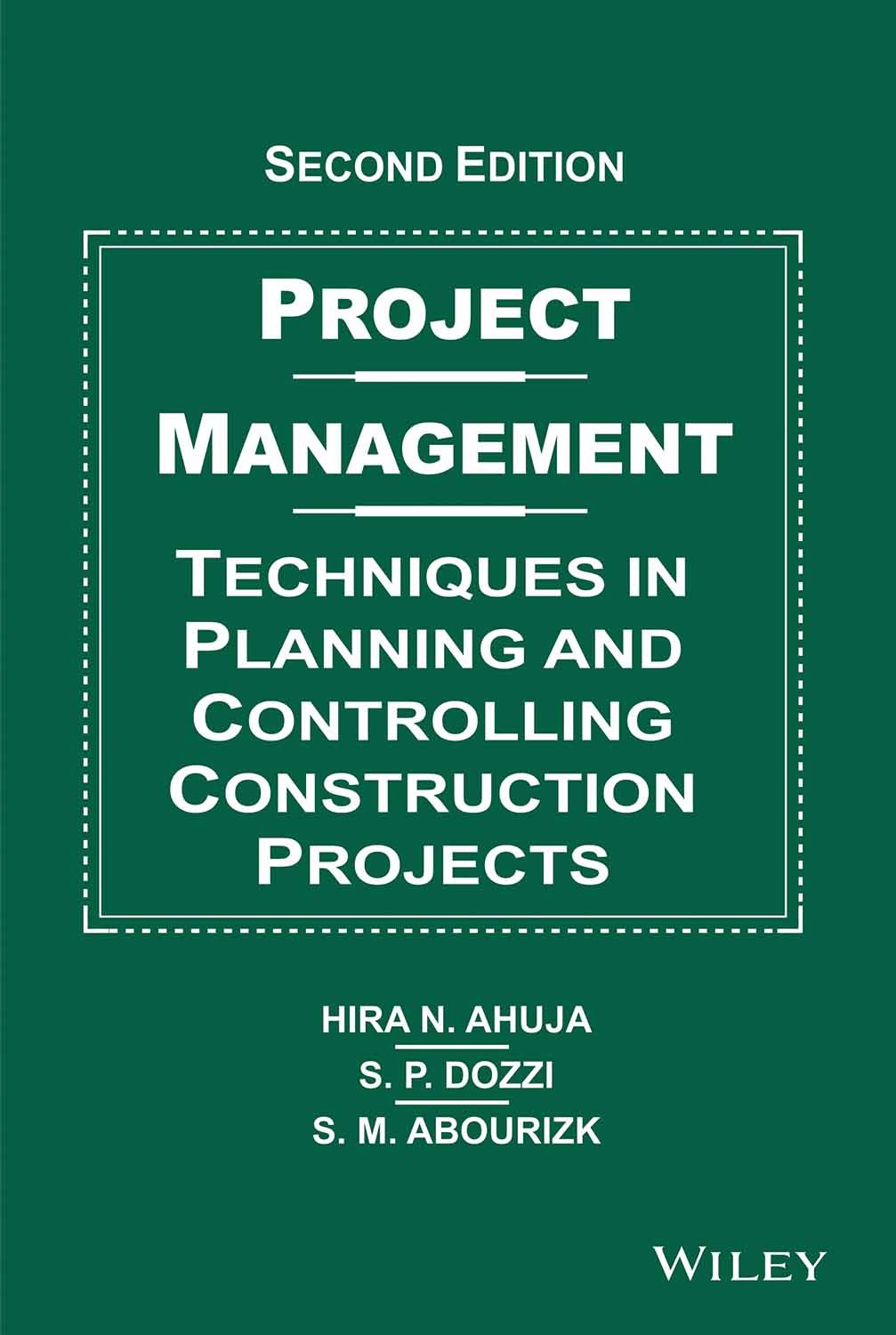
A WMS is a great way to manage inventory in your warehouses. It will help you determine the best layout for storage and workflow within your warehouse. Additionally, it will track all inventory so that you can better manage your supply chain. It can also be used to support serial numbers, bar-coding, RFID tags, or RFID tags. Some systems will even eliminate the need for periodic manual inventories, so you can focus on more important tasks.
Documentation flow
Documentation of logistics flow is essential for any business operation. It describes a company's business processes and is often an important reflection of minor actions. No matter the size of your logistics company, it is vital to its success. Without proper document management, even the most simple tasks can quickly turn into overwhelming tasks.
The documentation flow is crucial for the smooth flow and management of materials in the supply chains. It involves the active engagement of all parties. This includes all parties, including the 3PL, logistics carrier and buyer. You also need to have visibility and documentation flow. To ensure perfect logistics, documentation should be created before goods move.
Track and trace
Track and Trace logistics can reduce costs and improve product quality. Track and trace can be used to track your shipment from start to finish and prevent any tampering or faulty shipments. It can help improve the management of inventory and plan for your business. It will help you locate the products in your inventory, reduce redundant storage space and maximize fleet productivity.
Track and trace in logistics can help you maintain customer satisfaction which is an important aspect of any business. This will inform customers and give them accurate delivery times. You will be able to reduce the time spent searching for goods and decrease manual inventory checks.
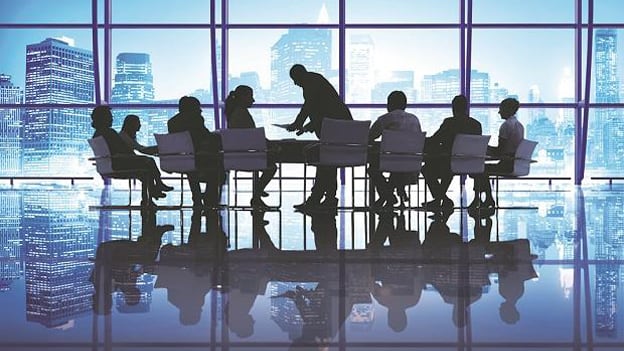
Asset control
Asset control refers to the process of tracking, monitoring, and securing inventory to meet customer requirements. It involves policies, procedures and organizational tools that help in the management of assets. This includes tracking all equipment and supplies. It requires regular physical inventories and the tracking of inventory level changes.
Asset management isn’t new. However, it’s becoming more important for companies all sizes. This process has seen a lot of modernization over the years. Companies don't need to use spreadsheets or notebooks for asset tracking. Now, asset management software can help businesses keep an up-to-date, complete visual inventory of their assets.
FAQ
What is the difference in Six Sigma and TQM?
The main difference in these two quality management tools lies in the fact that six sigma is focused on eliminating defects and total quality management (TQM), emphasizes improving processes and reducing costs.
Six Sigma is an approach for continuous improvement. It emphasizes the elimination or minimization of defects through statistical methods such control charts and p charts.
This method aims to reduce variation in product production. This is done by identifying and correcting the root causes of problems.
Total Quality Management involves monitoring and measuring every aspect of the organization. It also includes training employees to improve performance.
It is commonly used as a strategy for increasing productivity.
How do you manage employees effectively?
Achieving employee happiness and productivity is key to managing them effectively.
It is important to set clear expectations about their behavior and keep track of their performance.
Managers need to establish clear goals for their team and for themselves.
They must communicate clearly with their staff. They should also ensure that they both reward high performers and discipline those who are not performing to their standards.
They must also keep records of team activities. These include:
-
What was the result?
-
How much work was done?
-
Who did it?
-
What was the moment it was completed?
-
Why was it done?
This information can be used for monitoring performance and evaluating results.
What are the steps to take in order to make a management decision?
The decision-making process of managers is complicated and multifaceted. It involves many factors, including but not limited to analysis, strategy, planning, implementation, measurement, evaluation, feedback, etc.
Management of people requires that you remember that they are just as human as you are, and can make mistakes. As such, there is always room for improvement, especially if you're willing to put forth the effort to improve yourself first.
We explain in this video how the Management decision-making process works. We will explain the importance of different types decisions and how every manager can make them. The following topics will be covered.
What is the meaning of "project management?"
It refers to the management of activities related to a project.
This includes defining the scope, identifying the requirements and preparing the budget. We also organize the project team, schedule the work, monitor progress, evaluate results, and close the project.
Statistics
- The BLS says that financial services jobs like banking are expected to grow 4% by 2030, about as fast as the national average. (wgu.edu)
- Our program is 100% engineered for your success. (online.uc.edu)
- UpCounsel accepts only the top 5 percent of lawyers on its site. (upcounsel.com)
- As of 2020, personal bankers or tellers make an average of $32,620 per year, according to the BLS. (wgu.edu)
- Hire the top business lawyers and save up to 60% on legal fees (upcounsel.com)
External Links
How To
How is Lean Manufacturing done?
Lean Manufacturing processes are used to reduce waste and improve efficiency through structured methods. They were developed in Japan by Toyota Motor Corporation (in the 1980s). The aim was to produce better quality products at lower costs. Lean manufacturing seeks to eliminate unnecessary steps and activities in the production process. It has five components: continuous improvement and pull systems; just-in time; continuous change; and kaizen (continuous innovation). It is a system that produces only the product the customer requests without additional work. Continuous improvement is the continuous improvement of existing processes. Just-intime refers the time components and materials arrive at the exact place where they are needed. Kaizen stands for continuous improvement. Kaizen can be described as a process of making small improvements continuously. Fifth, the 5S stand for sort, set up in order to shine, standardize, maintain, and standardize. These five elements can be combined to achieve the best possible results.
Lean Production System
The lean production system is based on six key concepts:
-
Flow - The focus is on moving information and material as close as possible to customers.
-
Value stream mapping: This is a way to break down each stage into separate tasks and create a flowchart for the entire process.
-
Five S's - Sort, Set In Order, Shine, Standardize, and Sustain;
-
Kanban - use visual signals such as colored tape, stickers, or other visual cues to keep track of inventory;
-
Theory of constraints: Identify bottlenecks and use lean tools such as kanban boards to eliminate them.
-
Just-intime - Order components and materials at your location right on the spot.
-
Continuous improvement is making incremental improvements to your process, rather than trying to overhaul it all at once.