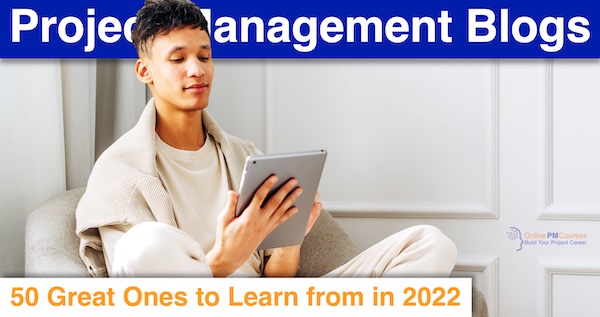
These are the fundamentals of management and organization. They govern how we plan, execute, and measure our efforts. These principles are derived from the works of classical economists like Adam Smith, John Stuart Mill, and Eli Whitney. Matthew Boulton (technical innovator) also contributed to this field.
Managing
Management's role is to ensure that all employees understand what they are doing and that everything runs smoothly. Management is essential to ensure that businesses succeed, no matter how large or small they may be. This program will be beneficial to junior managers and middle-level employees in small businesses, large corporations and government services.
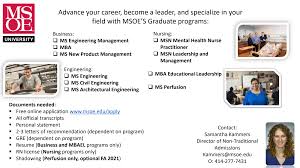
Monitoring
Monitoring is an important management practice that involves collecting, analyzing, and reporting data to measure progress and improve performance. It involves identifying targets and activities, as well as tracking the evolution of those activities over time. Managers and other stakeholders can use this information to quickly make decisions about the program's effectiveness.
Implementing
This paper discusses a process to implement change within organizations. Although small changes may be difficult to implement, they can be made if people are open to the idea. Youker's paper examines change resistance and outlines ways to improve acceptance. Youker also presents an analytical model for studying resistance to change.
Controlling
Controlling management and organizations is one of the primary functions of management. This function ensures that an organization's resources are efficiently used and that it meets its objectives. This function helps employees stay motivated by setting high performance standards and making sure that resources are used efficiently.
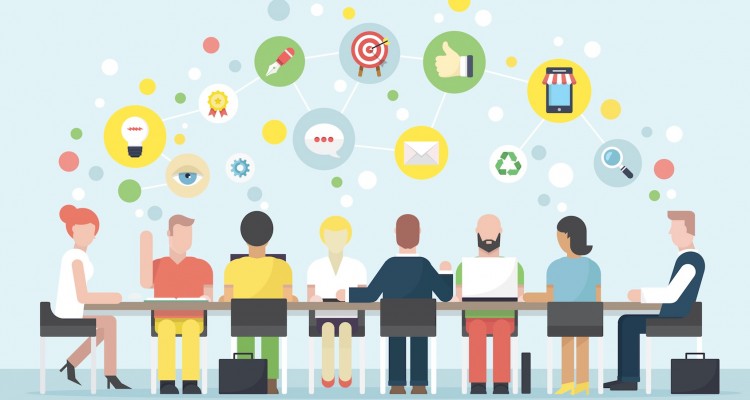
Maximal resource use
Resource management involves balancing the demand and supply in order to create a more productive company. If done correctly, resource management can increase profits and efficiency. This helps businesses operate more efficiently and consistently. In addition, resource management helps businesses rise above their competition.
FAQ
What are the 3 basic management styles?
There are three types of management: participative, laissez faire, and authoritarian. Each style has strengths and flaws. What style do you prefer? Why?
Autoritarian - The leader sets direction and expects everyone else to follow it. This style works best in large organizations that are stable and well-organized.
Laissez-faire - The leader allows each individual to decide for him/herself. This style is best when the organization has a small but dynamic group.
Participative – Leaders are open to suggestions and ideas from everyone. This style is most effective in smaller organizations, where everyone feels valued.
How does Six Sigma work?
Six Sigma employs statistical analysis to identify problems, measure them and analyze root causes. Six Sigma also uses experience to correct problems.
The first step in solving a problem is to identify it.
The next step is to collect data and analyze it in order to identify trends or patterns.
Then, corrective actions can be taken to resolve the problem.
Finally, data will be reanalyzed to determine if there is an issue.
This continues until the problem has been solved.
Why does it sometimes seem so difficult to make good business decisions?
Complex business systems have many moving parts. They require people to manage multiple priorities and deal with uncertainty and complexity.
To make good decisions, you must understand how these factors affect the entire system.
It is important to consider the functions and reasons for each part of the system. Then, you need to think about how these pieces interact with one another.
You need to ask yourself if your previous actions have led you to make unfounded assumptions. If they don't, you may want to reconsider them.
If you're still stuck after all this, try asking someone else for help. They might have different perspectives than you, and could offer insight that could help you solve your problem.
Statistics
- Your choice in Step 5 may very likely be the same or similar to the alternative you placed at the top of your list at the end of Step 4. (umassd.edu)
- The BLS says that financial services jobs like banking are expected to grow 4% by 2030, about as fast as the national average. (wgu.edu)
- This field is expected to grow about 7% by 2028, a bit faster than the national average for job growth. (wgu.edu)
- Our program is 100% engineered for your success. (online.uc.edu)
- Hire the top business lawyers and save up to 60% on legal fees (upcounsel.com)
External Links
How To
What is Lean Manufacturing?
Lean Manufacturing processes are used to reduce waste and improve efficiency through structured methods. They were developed in Japan by Toyota Motor Corporation (in the 1980s). The primary goal was to make products with lower costs and maintain high quality. Lean manufacturing focuses on eliminating unnecessary steps and activities from the production process. It is made up of five elements: continuous improvement, continuous improvement, just in-time, continuous change, and 5S. Pull systems involve producing only what the customer wants without any extra work. Continuous improvement means continuously improving on existing processes. Just-in-time is when components and other materials are delivered at their destination in a timely manner. Kaizen refers to continuous improvement. It is achieved through small changes that are made continuously. Five-S stands for sort. It is also the acronym for shine, standardize (standardize), and sustain. These five elements are used together to ensure the best possible results.
The Lean Production System
The lean production system is based on six key concepts:
-
Flow - The focus is on moving information and material as close as possible to customers.
-
Value stream mapping is the ability to divide a process into smaller tasks, and then create a flowchart that shows the entire process.
-
Five S's, Sort, Set in Order, Shine. Standardize. and Sustain.
-
Kanban – visual signals like colored tape, stickers or other visual cues are used to keep track inventory.
-
Theory of constraints - identify bottlenecks during the process and eliminate them with lean tools like Kanban boards.
-
Just-in time - Get components and materials delivered right at the point of usage;
-
Continuous improvement - make incremental improvements to the process rather than overhauling it all at once.