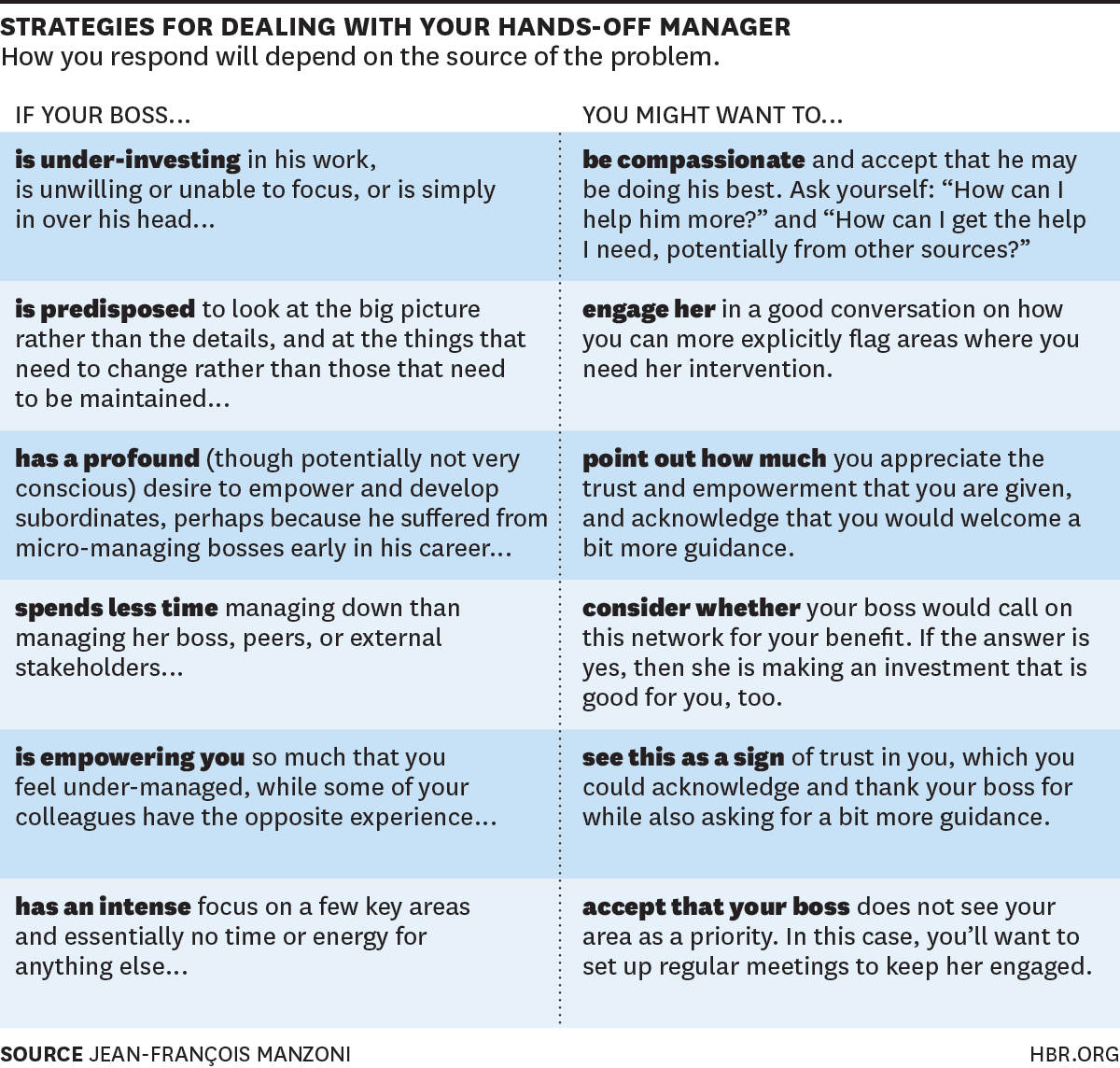
A business flow measurement does not take into account the inherent directionality, or even directionality, of supply networks. Supply networks are complex and have many dependencies. These dependencies can often be interrelated. Further, a business flow measure does not reflect the natural directionality in information flows within a given network. These are the issues that must be considered when developing a digital supply system.
Sustainability
Sustainability of supply networks is a critical element of the supply chain management strategy of multinational corporations. Many companies have made sustainability an important priority and committed themselves to using sustainable suppliers. There are serious risks for businesses if lower-ranking suppliers do not comply with sustainability standards. This article examines three major MNCs' supply networks. The authors found some best practices that companies could adopt to counter this problem. These include including lower-tier suppliers into the sustainability strategy and setting long-term sustainability objectives.
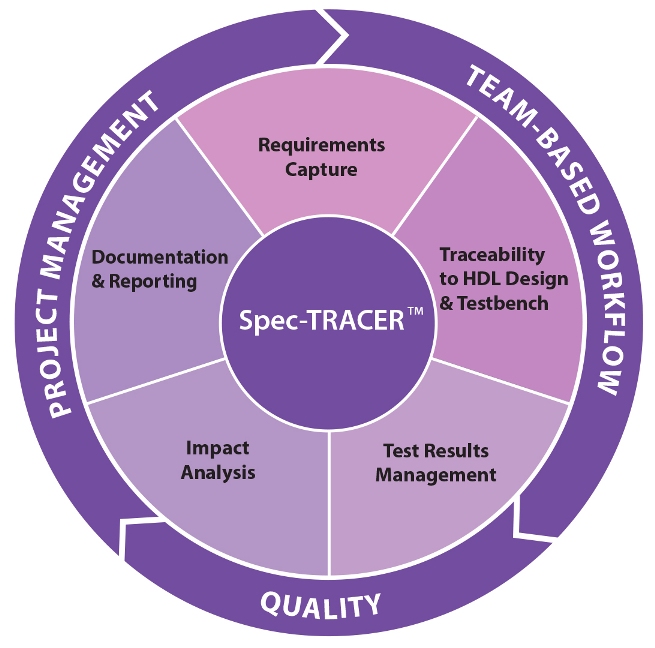
Companies need to set targets and measure progress to demonstrate how they are improving their supply chains. They must engage all parties in the supply chain including consumers and internal staff. The goal should be to highlight the business benefits associated with sustainable supply networks, and to establish proper governance and organizational structure to ensure that sustainability efforts are a success.
Vertical disintegration in supply chains
The potential for vertical disintegration within supply chains can have several consequences for companies. It can lead to organizational changes and hierarchies, as well as higher costs and loss. Companies may decide to reduce their involvement and participation in downstream or upstream activities in order to improve their overall competitiveness. However, this approach is not always appropriate and should only be implemented in specific circumstances.
Vertical integration has the disadvantage that it reduces flexibility. This is because it forces it to follow trends within a particular segment. For example, it may be difficult for a retailer to adopt a new technology because its competition has already adopted it. If this were the case, the parent company would have to invest in the new technology to keep up with the competition. Rapidly changing technologies can make integration difficult. Companies often have to integrate different technologies from different supply chains. This can prove costly.
A digital supply network can have performance implications
Digital supply chains offer many benefits including cost savings, increased efficiency, resilience and cost savings. They can also pose cybersecurity risks. However, there are many options companies have to minimize these risks. Let's look at some. These methods rely on data analytics. This technology gives businesses insight into customer preferences and allows them to improve their products. Also, by incorporating shared data from various sources, companies can predict potential problems and make better, more informed decisions.
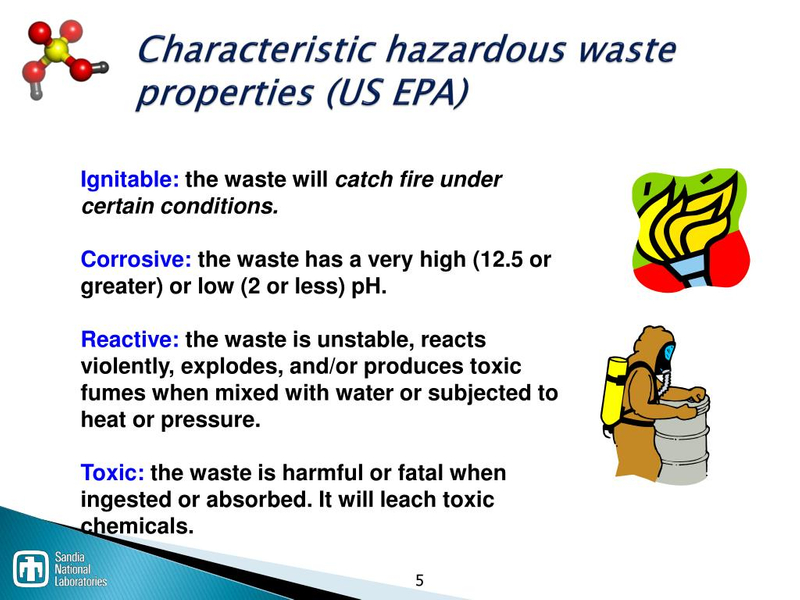
The first step in implementing digitalization is to assess your existing supply chain. This will help you understand any existing issues or risks, as well as any potential complications. Once you have this information, you can create an action program to minimize risks. Once you have a clear picture of your goals, it is time to work with your partner. This will ensure that all stakeholders are satisfied with the digital supply chain.
FAQ
What's the difference between Six Sigma and TQM?
The major difference between the two tools for quality management is that six Sigma focuses on eliminating defect while total quality control (TQM), on improving processes and decreasing costs.
Six Sigma is an approach for continuous improvement. This approach emphasizes eliminating defects through statistical methods like control charts, Pareto analysis, and p-charts.
This method has the goal to reduce variation of product output. This is accomplished through identifying and correcting root causes.
Total quality management includes monitoring and measuring all aspects of an organization's performance. This includes training employees to improve their performance.
It is often used to increase productivity.
What is Kaizen and how can it help you?
Kaizen is a Japanese term meaning "continuous improvement." It is a philosophy that encourages employees to constantly look for ways to improve their work environment.
Kaizen is based on the belief that every person should be able to do his or her job well.
What is TQM and how can it help you?
The industrial revolution saw the realization that prices alone were not sufficient to sustain manufacturing companies. This led to the birth of quality. If they wanted to stay competitive, they needed to improve their quality and efficiency.
In response to this need for improvement, management developed Total Quality Management (TQM), which focused on improving all aspects of an organization's performance. It included continuous improvement processes, employee involvement, and customer satisfaction.
Why is it important for companies to use project management techniques?
Project management techniques ensure that projects run smoothly while meeting deadlines.
This is due to the fact that most businesses rely heavily upon project work in order to produce goods, and services.
Companies need to manage these projects efficiently and effectively.
Companies that do not manage their projects effectively risk losing time, money, or reputation.
What is the role of a manager in a company?
There are many roles that a manager can play in different industries.
A manager is generally responsible for overseeing the day to day operations of a company.
He/she makes sure that the company meets its financial obligations, and that it produces goods or services that customers desire.
He/she will ensure that employees follow all rules and regulations, and adhere to quality standards.
He/she plans and oversees marketing campaigns.
How does a manager develop his/her management skills?
It is important to have good management skills.
Managers should monitor the performance and progress of their subordinates.
You must act quickly if you notice that your subordinate isn’t performing to their standards.
You should be able pinpoint what needs to improve and how to fix it.
Statistics
- The profession is expected to grow 7% by 2028, a bit faster than the national average. (wgu.edu)
- UpCounsel accepts only the top 5 percent of lawyers on its site. (upcounsel.com)
- The BLS says that financial services jobs like banking are expected to grow 4% by 2030, about as fast as the national average. (wgu.edu)
- The average salary for financial advisors in 2021 is around $60,000 per year, with the top 10% of the profession making more than $111,000 per year. (wgu.edu)
- Hire the top business lawyers and save up to 60% on legal fees (upcounsel.com)
External Links
How To
How do you apply the Kaizen method to your life?
Kaizen means continuous improvement. This Japanese term refers to the Japanese philosophy of continuous improvement that emphasizes incremental improvements and constant improvement. It's a process where people work together to improve their processes continuously.
Kaizen is one method that Lean Manufacturing uses to its greatest advantage. Employees responsible for the production line should identify potential problems in the manufacturing process and work together to resolve them. This improves the quality of products, while reducing the cost.
Kaizen is a way to raise awareness about what's happening around you. To prevent problems from happening, any problem should be addressed immediately. If someone is aware of a problem at work, he/she should inform his/her manager immediately.
There are some basic principles that we follow when doing kaizen. Always start with the end product in mind and work our way back to the beginning. We can improve the factory by first fixing the machines that make it. Then, we fix the machines that produce components and then the ones that produce raw materials. Then, we fix those who work directly with the machines.
This is why it's called "kaizen" because it works step-by-step to improve everything. Once we have finished fixing the factory, we return to the beginning and work until perfection.
To implement kaizen in your business, you need to find out how to measure its effectiveness. There are several ways that you can tell if your kaizen system is working. One method is to inspect the finished products for defects. Another way to find out how productive your company has been since you implemented kaizen is to measure the increase in productivity.
If you want to find out if your kaizen is actually working, ask yourself why. Did you do it because it was legal or to save money? Did you really think that it would help you achieve success?
If you answered yes to any one of these questions, congratulations! You are ready to start kaizen.