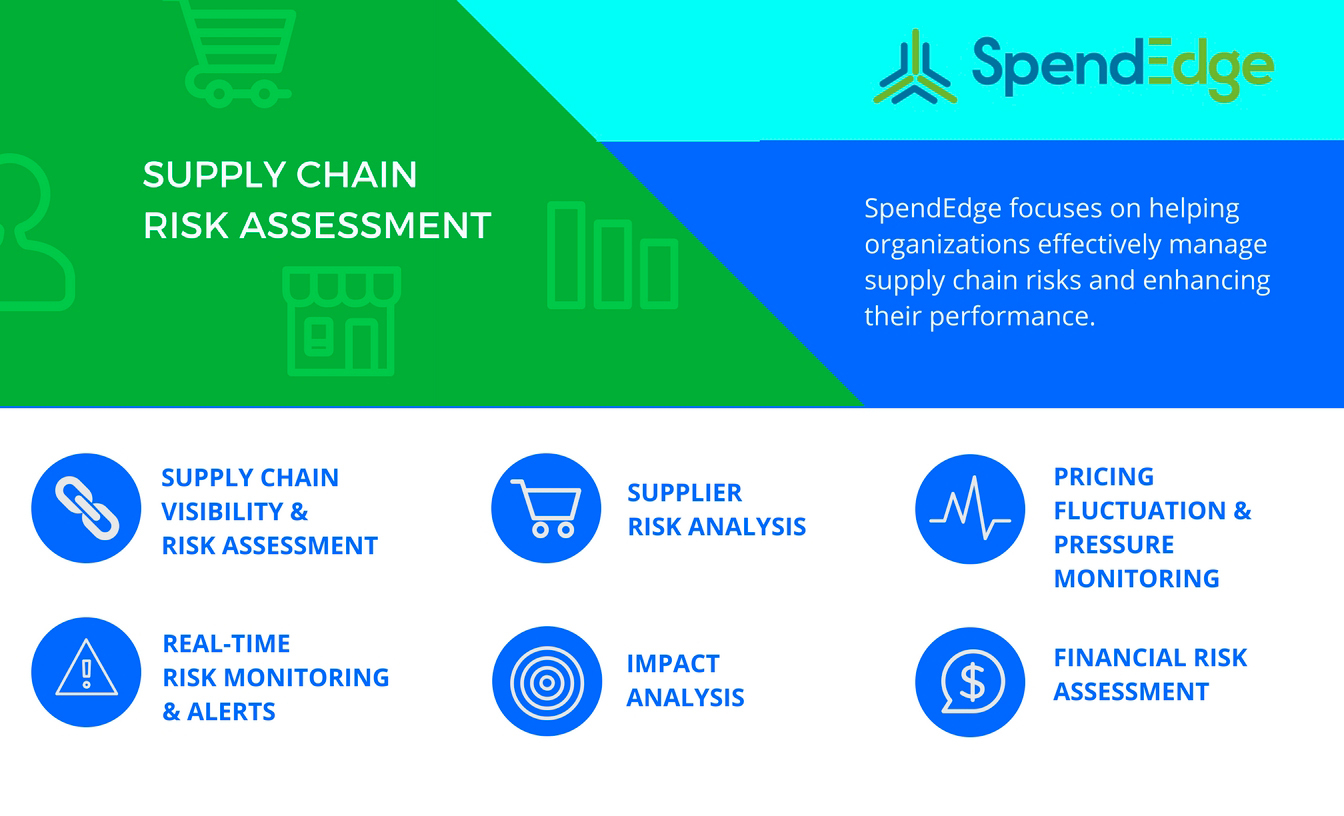
Process safety management is a disciplined approach to the management of the integrity of processes and operating systems in a facility. This system must be maintained at least once every five years and is required by law for major hazard facilities. Process safety management is designed to prevent accidents. Here are the steps to get you started in process safety management. These steps will make your facility as safe as possible, and prevent accidents.
Process safety management can be described as a disciplined framework that manages the integrity of operating system and process processes.
Process safety management aims to lower the risk of accidents and increase productivity. It involves minimizing risks and inherently safer equipment. It requires strict adherence and assessment of hazards. It also includes training and maintenance of the plant, including effective and disciplined process control. It is an essential element of a safety-conscious business.
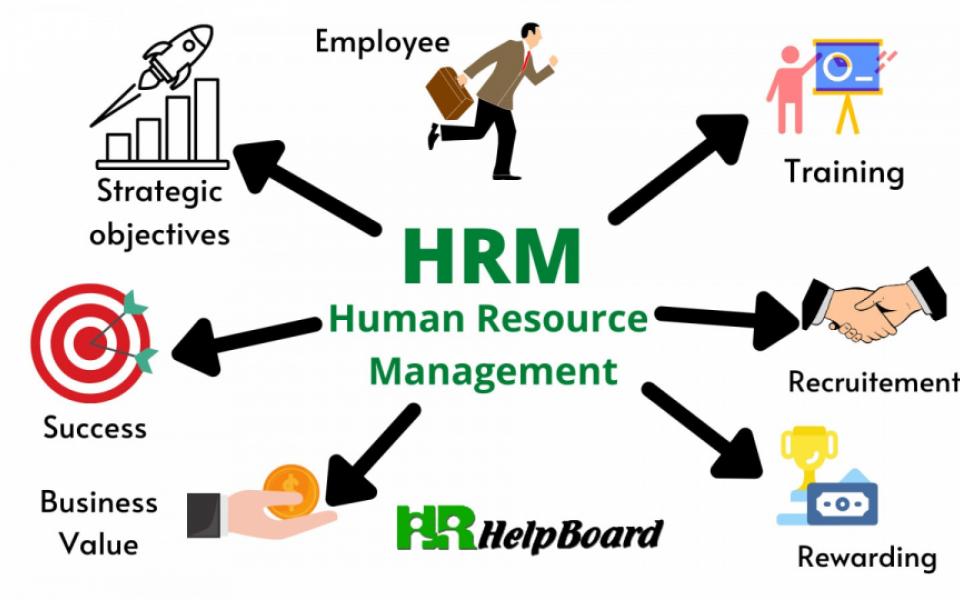
It should be up-to-date every five years
OSHA's Occupational Safety and Health Administration (OSHA), requires that processes are regularly reviewed and revised. This includes the development of written procedures and process safety information. All employees who are involved in the project must have this information. Written investigation reports, procedures, and other documents must be kept for 5 years. Employees must be able to access and follow up on updated process safety information. An employer may seek out safety risk management consulting to help them meet their requirements.
It is a requirement of law for major hazards facilities
All major hazards facilities must have a process safety management system. In addition to developing and implementing the program, employers must implement a procedure for a prompt and safe evacuation of employees. Most cases, the plan will include a safety alarm to alert employees to evacuate. Employees who are physically unable or unwilling to evacuate the hazardous area should be included in this plan.
It helps to prevent incidents
A well-designed process safety management system can increase a company’s profitability, safety performance, quality, and safety. It can also enhance the company's environmental accountability. Additionally, it reduces incidents. These four areas are vital for the long-term success of a company. Here is a quick overview of the many benefits of a process safety system. It helps companies prevent accidents and increase the safety and health of their employees and customers.
It takes a lot of time.
The process safety management of hazardous chemical facilities can be complex and time-consuming. Even if OSHA doesn't regulate process safety management programs, it does require facilities to have a written plan for implementation and to meet 14 minimum requirements. Some companies rely heavily on spreadsheets, forms and forms to collect information and compile risk analyses and other information. This is tedious and can result in human error.
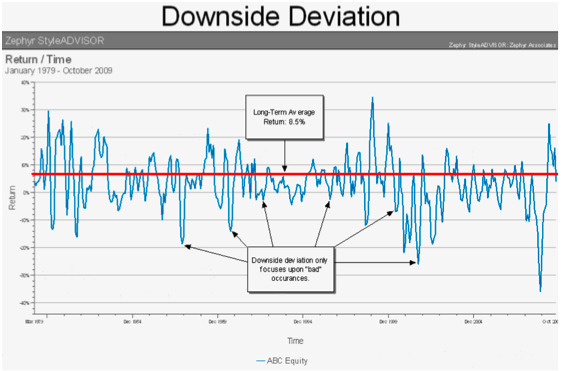
It requires employee participation
The Pennsylvania State University adopted a PSM program that includes an Employee Participation element. This element leverages employees' knowledge, experience, and unique perspectives to improve safety. The program provides information about the different participation mechanisms and minimum requirements. It is important to include all employees in the process safety management process and involve them in all aspects. Employee participation in PSM is essential to avoiding serious incidents. How can you make sure that everyone is involved in the program?
FAQ
What are management principles?
Management concepts are the fundamental principles and practices that managers use when managing people and their resources. These topics include job descriptions, performance evaluations and training programs. They also cover human resource policies, job description, job descriptions, job descriptions, employee motivation, compensation systems, organizational structures, and many other topics.
What are some common mistakes managers make?
Sometimes managers make their job harder than they need to.
They may not assign enough responsibilities to staff members and provide them with inadequate support.
A majority of managers lack the communication skills needed to motivate their team and lead them.
Some managers create unrealistic expectations for their teams.
Managers may prefer to solve every problem for themselves than to delegate responsibility.
It can sometimes seem difficult to make business decisions.
Businesses are complex systems, and they have many moving parts. Their leaders must manage multiple priorities, as well as dealing with uncertainty.
The key to making good decisions is to understand how these factors affect the system as a whole.
This requires you to think about the purpose and function of each component. You then need to consider how those individual pieces interact with each other.
You should also ask yourself if there are any hidden assumptions behind how you've been doing things. If you don't have any, it may be time to revisit them.
If you're still stuck after all this, try asking someone else for help. They might have different perspectives than you, and could offer insight that could help you solve your problem.
What is Six Sigma?
It's a method for quality improvement that focuses on customer service as well as continuous learning. The goal is to eliminate defects by using statistical techniques.
Motorola created Six Sigma as part of their efforts to improve manufacturing processes in 1986.
The idea spread quickly throughout the industry, and today, many organizations are using six sigma methods to improve product design, production, delivery, and customer service.
What are the four major functions of Management?
Management is responsible for organizing, managing, directing and controlling people, resources, and other activities. It includes the development of policies and procedures as well as setting goals.
Management helps an organization achieve its objectives by providing direction, coordination, control, leadership, motivation, supervision, training, and evaluation.
These are the four major functions of management:
Planning - Planning refers to deciding what is needed.
Organizing: Organizing refers to deciding how things should work.
Direction - This is the art of getting people to follow your instructions.
Controlling - This is the ability to control people and ensure that they do their jobs according to plan.
Statistics
- The profession is expected to grow 7% by 2028, a bit faster than the national average. (wgu.edu)
- UpCounsel accepts only the top 5 percent of lawyers on its site. (upcounsel.com)
- Our program is 100% engineered for your success. (online.uc.edu)
- This field is expected to grow about 7% by 2028, a bit faster than the national average for job growth. (wgu.edu)
- 100% of the courses are offered online, and no campus visits are required — a big time-saver for you. (online.uc.edu)
External Links
How To
How does Lean Manufacturing work?
Lean Manufacturing methods are used to reduce waste through structured processes. These processes were created by Toyota Motor Corporation, Japan in the 1980s. The aim was to produce better quality products at lower costs. Lean manufacturing is about eliminating redundant steps and activities from the manufacturing process. It consists of five basic elements: pull systems, continuous improvement, just-in-time, kaizen (continuous change), and 5S. Pull systems are able to produce exactly what the customer requires without extra work. Continuous improvement means continuously improving on existing processes. Just-in–time refers when components or materials are delivered immediately to their intended destination. Kaizen is continuous improvement. This can be achieved by making small, incremental changes every day. The 5S acronym stands for sort in order, shine standardize and maintain. These five elements work together to produce the best results.
The Lean Production System
Six key concepts make up the lean manufacturing system.
-
Flow is about moving material and information as near as customers can.
-
Value stream mapping - Break down each stage in a process into distinct tasks and create an overview of the whole process.
-
Five S's, Sort, Set in Order, Shine. Standardize. and Sustain.
-
Kanban - visual cues such as stickers or colored tape can be used to track inventory.
-
Theory of constraints: Identify bottlenecks and use lean tools such as kanban boards to eliminate them.
-
Just-in-time - deliver components and materials directly to the point of use;
-
Continuous improvement: Make incremental improvements to the process instead of overhauling it completely.