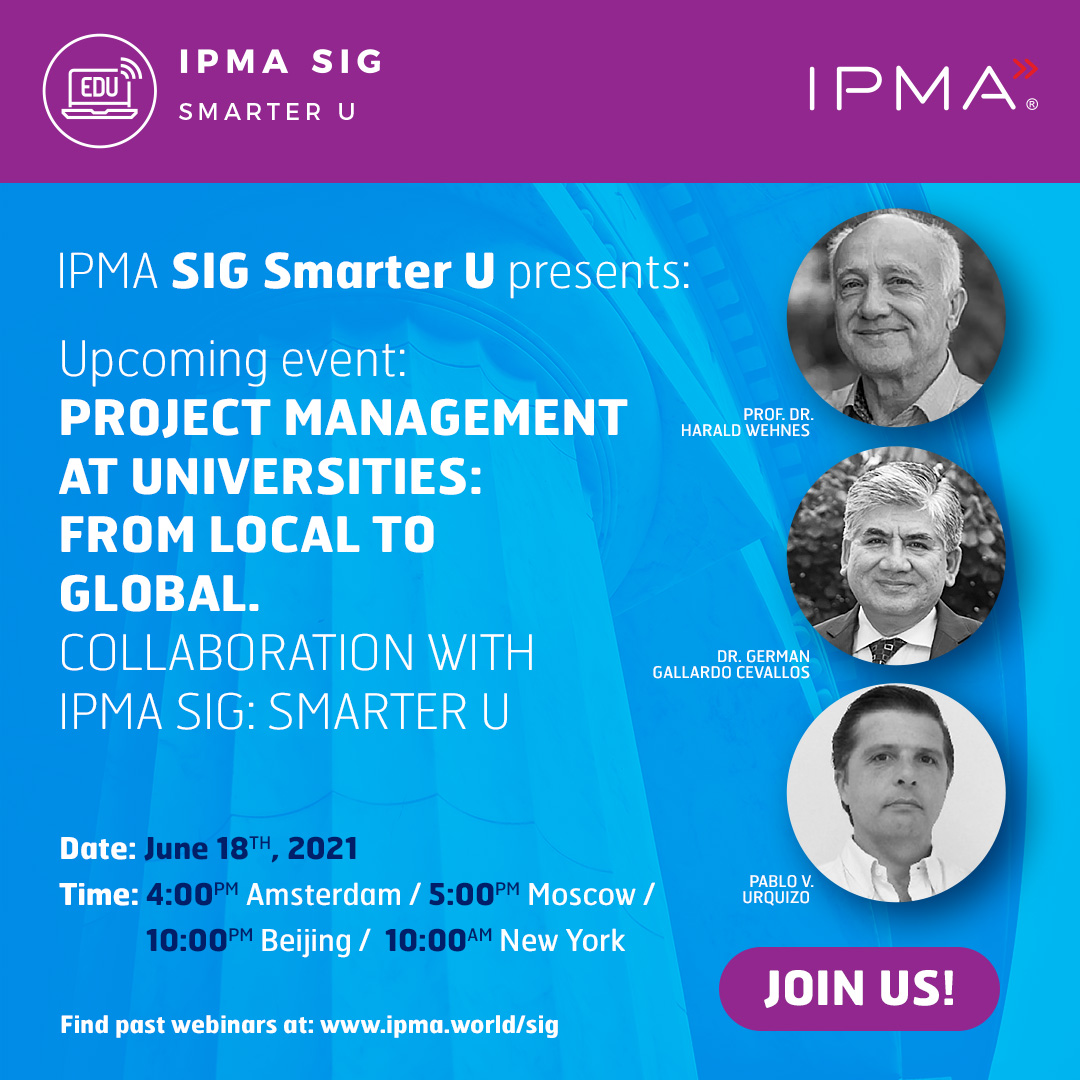
Process knowledge management is an essential tool in quality and risk management. It helps to connect past knowledge to current information, as well as data from previous products. It can also be used to support continuous improvement. Let's take a look at some benefits of process information management. Here are some. You might be amazed at how beneficial it can be for your business. It's also easy to put into practice.
Lessons learned
Ideally, your organisation will have a template for lessons learned and make this readily available to all employees. It is better to use a document manager system to share the lessons you have learned with your staff. Although the template should be clear and easy to comprehend by your team, you should consider trying different formats. You can make your employees resist sharing complicated documents. You must choose the most appropriate format to engage your staff.
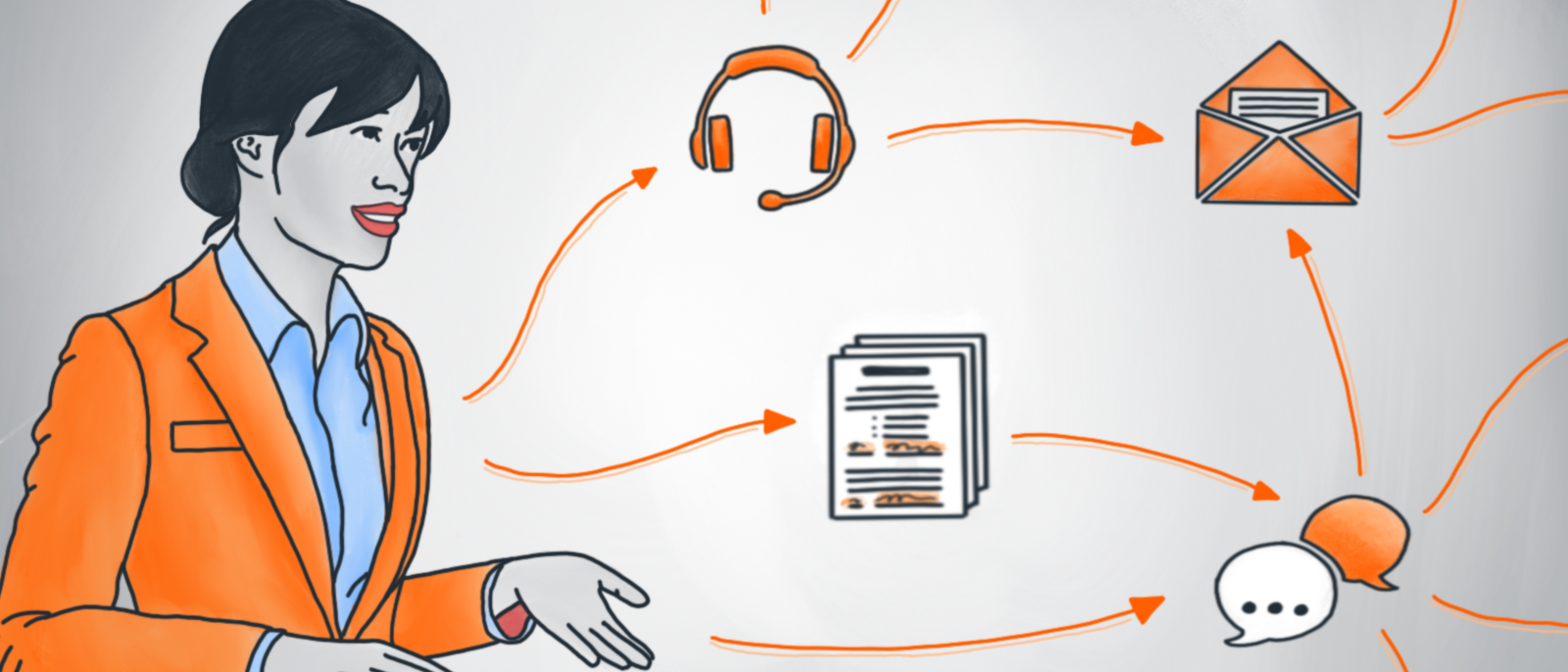
Expertise location
Expert location is much more than just biographical details. It allows you to share your knowledge and find the right employees to answer your questions. Most people have a LinkedIn, Facebook, and Google+ profile that includes their expertise. These tools also structure information for people by giving them places to describe their projects, publications, and knowledge. This can help them build their reputation and increase their visibility.
Communities & network
The creation of virtual communities can facilitate cross-industry collaborations as well as strategic knowledge management. These communities can foster communication and dissemination of new approaches, processes, and tools that help to improve performance and innovation in organisations. They can be used to improve the effectiveness of meetings and share case histories. A number of industry leaders are exploring the benefits of using communities in industrial manufacturing. See Communities and networks for process knowledge management for more information. These networks provide a framework for knowledge management. They are meant to bring together people from different disciplines or locations.
Content management
While a content-management system can store a training document with 200 pages of information, it cannot replace a knowledge management system that can capture institutional and user-generated knowledge about a specific topic. This system should be able to capture information from multiple perspectives. This can help customers make better decisions and serve them better. For example, a content management system can store all materials used in training sales personnel for a dealership that sells cars.
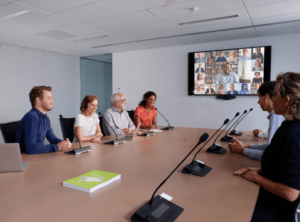
Knowledge mapping
Knowledge mapping is a great way to leverage your knowledge assets and improve your processes. Knowledge mapping can be a powerful tool to identify gaps in knowledge and help you create better processes. It is also an excellent tool for increasing collaboration and engagement among departments. Once you have mapped out your knowledge, you can begin to standardize processes. Knowledge maps are a great tool for capturing and disseminating best practices and improving your organization's operations.
FAQ
What are your main management skills
Management skills are essential for any business owner, whether they're running a small local store or an international corporation. These skills include the ability of managing people, finances, time, space, and other factors.
When you need to manage people, set goals, lead teams, motivate them, solve problems, develop policies and procedures and manage change, management skills are essential.
You can see that there are many managerial duties.
What are the steps in the decision-making process in management?
Managers have to make complex decisions. It involves many factors, such as analysis and strategy, planning, execution, measurement, evaluation, feedback etc.
It is important to remember that people are human beings, just like you. They make mistakes. You are always capable of improving yourself, and there's always room for improvement.
In this video, we explain what the decision-making process looks like in Management. We discuss the different types of decisions and why they are important, every manager should know how to navigate them. The following topics will be covered:
What's the difference between leadership & management?
Leadership is about inspiring others. Management is about controlling others.
A leader inspires others while a manager directs them.
A leader inspires others to succeed, while a manager helps workers stay on task.
A leader develops people; a manager manages people.
What is the difference in Six Sigma and TQM?
The major difference between the two tools for quality management is that six Sigma focuses on eliminating defect while total quality control (TQM), on improving processes and decreasing costs.
Six Sigma is an approach for continuous improvement. It emphasizes the elimination or minimization of defects through statistical methods such control charts and p charts.
The goal of this method is to reduce variation in product output. This is done by identifying root causes and rectifying them.
Total quality management involves measuring and monitoring all aspects of the organization. This includes training employees to improve their performance.
It is often used to increase productivity.
Statistics
- This field is expected to grow about 7% by 2028, a bit faster than the national average for job growth. (wgu.edu)
- As of 2020, personal bankers or tellers make an average of $32,620 per year, according to the BLS. (wgu.edu)
- Hire the top business lawyers and save up to 60% on legal fees (upcounsel.com)
- UpCounsel accepts only the top 5 percent of lawyers on its site. (upcounsel.com)
- Your choice in Step 5 may very likely be the same or similar to the alternative you placed at the top of your list at the end of Step 4. (umassd.edu)
External Links
How To
How can you implement the Kaizen technique?
Kaizen means continuous improvement. The term was coined in the 1950s at Toyota Motor Corporation and refers to the Japanese philosophy emphasizing constant improvement through small incremental changes. It's where people work together in order to improve their processes constantly.
Kaizen is one of the most effective methods used in Lean Manufacturing. The concept involves employees responsible for manufacturing identifying problems and trying to fix them before they become serious issues. This way, the quality of products increases, and the cost decreases.
Kaizen is a way to raise awareness about what's happening around you. So that there is no problem, you should immediately correct it if something goes wrong. Report any problem you see at work to your manager.
Kaizen has a set of basic principles that we all follow. When working with kaizen, we always start with the end result and move towards the beginning. To improve our factory, for example, we need to fix the machines that produce the final product. First, we fix machines that produce components. Next, we fix machines that produce raw material. Then we fix the workers, who directly work with these machines.
This method, called 'kaizen', focuses on improving each and every step of the process. After we're done with the factory, it's time to go back and fix the problem.
Before you can implement kaizen into your business, it is necessary to learn how to measure its effectiveness. There are several ways that you can tell if your kaizen system is working. One method is to inspect the finished products for defects. Another way is determining how much productivity increased after implementing kaizen.
If you want to find out if your kaizen is actually working, ask yourself why. Was it just because it was the law or because you wanted to save money? Did you really think that it would help you achieve success?
Suppose you answered yes to any of these questions, congratulations! Now you're ready for kaizen.