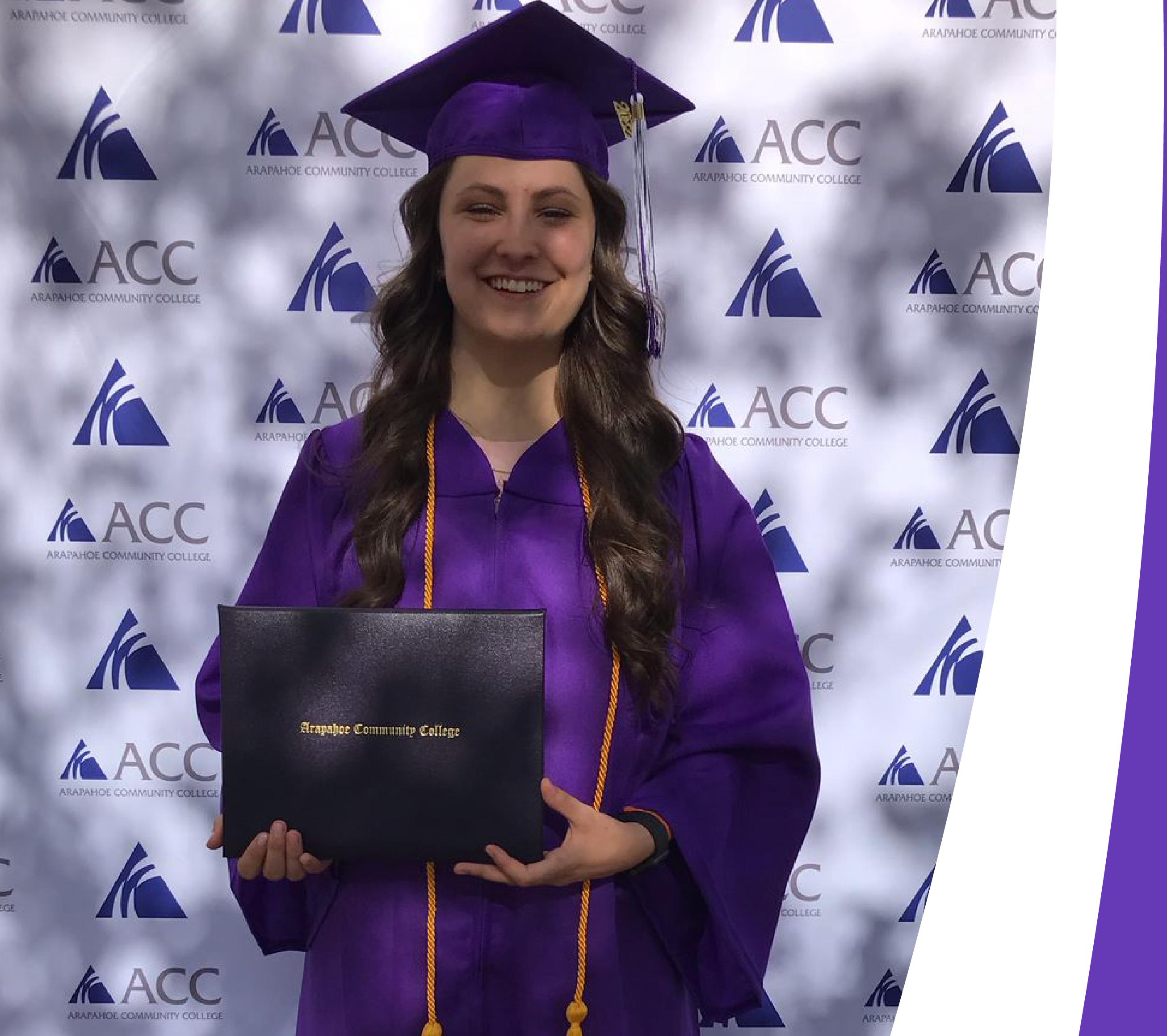
Management is the ability to make decisions and manage tasks in order to achieve a goal. This article will define how to manage different tasks, including creating and maintaining a positive internal environment and convincing others to achieve a goal. Managemnet is the act of getting things done with people who aren't necessarily organized into groups. Here are some common tasks people may have to deal with. These are the tasks:
Management is the coordination or administration of tasks that lead to a goal.
Management can be defined in many ways depending on the industry and the workplace. Management involves setting the strategy of an organization and coordinating the efforts of staff. Management also includes the management of senior staff. Management includes also the management of resources. Despite differences in each role, there are some common traits. These are some examples for management roles:
It requires creating an internal environment
The environment within a business organization is determined by seven things. These include the organization's values system, its mission, and goals, the organizational structure, the style and management of top executives, the quality of employees, labour unions, and its physical resources. Beyond these, the firm's internal environment has a significant impact on its decision making. An organization's success depends on its ability to create a culture that encourages innovation and allows employees to make smart decisions.
It involves convincing someone/something to get a result
Persuasion describes the art of convincing someone/something else to do something. While it can be challenging, it can also work in some situations. Below are some tips to help persuade others. These tips are worth trying:
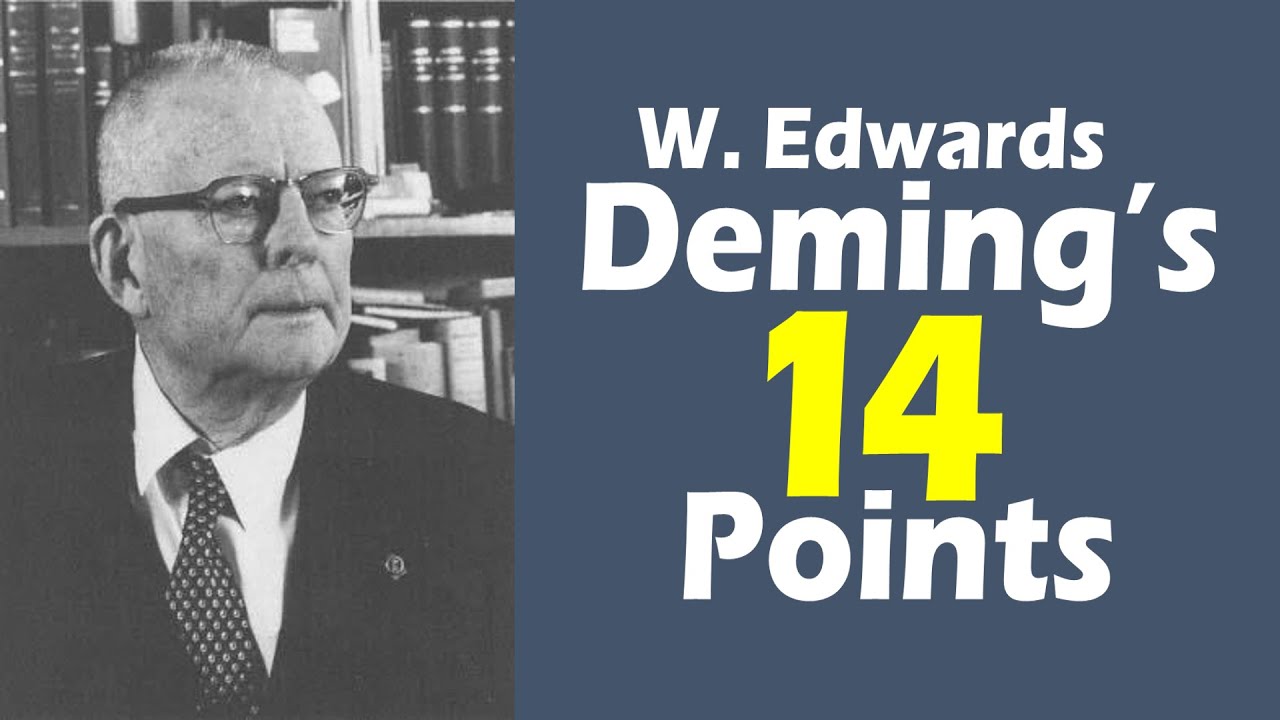
It involves getting things done with those informally organized groups
Management is the art of getting things done with and through people in a group. Informally organized groups are the backbone for a business while formal organizations are its brains. The former facilitates the company's normal production procedures, while whereas the latter takes over when an unexpected problem arises. This theory is based in part on Harold Koontz, an American organizational thinker.
FAQ
What is TQM exactly?
The industrial revolution saw the realization that prices alone were not sufficient to sustain manufacturing companies. This led to the birth of quality. They needed to improve quality and efficiency if they were going to remain competitive.
In response to this need for improvement, management developed Total Quality Management (TQM), which focused on improving all aspects of an organization's performance. It included continual improvement processes, employee involvement, customer satisfaction, and customer satisfaction.
What are the main four functions of management
Management is responsible in planning, organizing and directing people and resources. It includes creating policies and procedures, as well setting goals.
Management assists an organization in achieving its goals by providing direction, coordination and control, leadership, motivation, supervision and training, as well as evaluation.
Management has four primary functions:
Planning - This is the process of deciding what should be done.
Organizing: Organizing refers to deciding how things should work.
Directing – This means to get people to follow directions.
Controlling: Controlling refers to making sure that people do what they are supposed to.
Why is it so important for companies that they use project management techniques
Project management techniques ensure that projects run smoothly while meeting deadlines.
This is because many businesses depend heavily upon project work to produce products and services.
These projects are essential for companies.
Companies may lose their reputation, time and money if they do not have effective project management.
How can a manager enhance his/her leadership skills?
By practicing good management skills at all times.
Managers need to monitor their subordinates' performance.
You must act quickly if you notice that your subordinate isn’t performing to their standards.
It is important to be able identify areas that need improvement and what can be done to improve them.
What role does a manager play in a company?
Different industries have different roles for managers.
A manager is generally responsible for overseeing the day to day operations of a company.
He/she is responsible for ensuring that the company meets all its financial obligations and produces the goods or services customers want.
He/she will ensure that employees follow all rules and regulations, and adhere to quality standards.
He/she plans new products and services and oversees marketing campaigns.
Statistics
- Your choice in Step 5 may very likely be the same or similar to the alternative you placed at the top of your list at the end of Step 4. (umassd.edu)
- UpCounsel accepts only the top 5 percent of lawyers on its site. (upcounsel.com)
- The profession is expected to grow 7% by 2028, a bit faster than the national average. (wgu.edu)
- The average salary for financial advisors in 2021 is around $60,000 per year, with the top 10% of the profession making more than $111,000 per year. (wgu.edu)
- As of 2020, personal bankers or tellers make an average of $32,620 per year, according to the BLS. (wgu.edu)
External Links
How To
How do I do the Kaizen Method?
Kaizen means continuous improvement. The Japanese philosophy emphasizes small, incremental improvements to achieve continuous improvement. This term was created by Toyota Motor Corporation in 1950. It's a process where people work together to improve their processes continuously.
Kaizen is one of Lean Manufacturing's most efficient methods. Kaizen is a concept where employees in charge of the production line are required to spot problems during the manufacturing process before they become major issues. This improves the quality of products, while reducing the cost.
Kaizen is an approach to making every worker aware and alert to what is happening around them. To prevent problems from happening, any problem should be addressed immediately. If someone spots a problem while at work, they should immediately report it to their manager.
There are some basic principles that we follow when doing kaizen. We always start from the end product and move toward the beginning. In order to improve our factory's production, we must first fix the machines producing the final product. First, we fix machines that produce components. Next, we fix machines that produce raw material. And finally, we fix the workers who work directly with those machines.
This is why it's called "kaizen" because it works step-by-step to improve everything. Once the factory is fixed, we return to the original site and work our way back until we get there.
How to measure kaizen's effectiveness in your business is essential to implement it. There are several ways that you can tell if your kaizen system is working. One way is to examine the amount of defects on the final products. Another way is to see how much productivity has increased since implementing kaizen.
Another way to know whether kaizen is working is to ask yourself why did you decide to implement kaizen. You were trying to save money or obey the law? Did you really believe that it would be a success factor?
If you answered yes to any one of these questions, congratulations! You're ready to start kaizen.