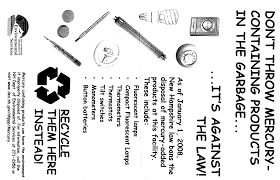
A common failure in managing risk is the lack of transparency. This was clearly demonstrated by the scandal surrounding coronavirus-related deaths. Data silos and a lack of data are other issues. The process was not built with risk in view. Risk managers are often tempted to accept the data that they have at their fingertips and neglect to identify potential risks that could result in negative consequences. This is a common problem that is difficult to fix, but should be avoided.
Negative risks
Managers can use five key risk management strategies to deal with threats and negative risks. These strategies depend on the kind of risk and the exposure level. They are dependent on the probability of occurrence as well as the impact that the risk will have. Avoidance and mitigation strategies are the most efficient and should be used when there are high-risk areas. If the risk is not so critical, then the transfer and acceptance strategy is recommended.
Positive and negative risks affect people, processes, technology, and resources. If managed properly, even positive risks can produce positive results. Positive risks can lead to a project's ending sooner than expected or higher returns on investment. Negative risks are possible in all situations. If you implement the right risk management strategies, you can prevent a negative risk. These risks can also pose challenges and affect the project's budget, schedule, and schedule.
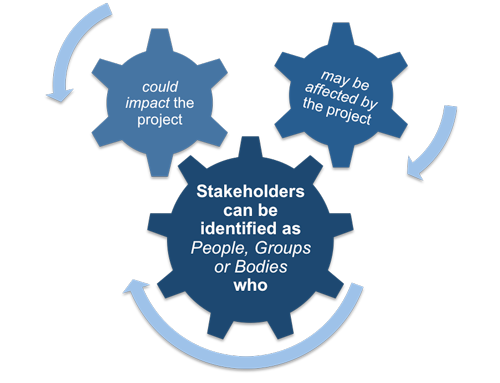
Communication
Communication is an essential part of risk management. Communicating risks to others, whether through a formal document (or via social media) is crucial. Professionals must be transparent and open with their clients. Communication professionals can help reduce misinterpretation of the risk. Hurricane Harvey is a simple example of how to communicate risk. In 2017, Hurricane Harvey was a devastating hurricane that threatened Houston. Public officials used social media and national communication to notify residents to evacuate. The professionals need to direct people to reliable sources of information.
Poor communication is one risk in project management. If there is poor communication, it can make or break a project. Communication can boost employee engagement as well as reduce miscommunications. A project's management risk assessment should include activities that improve communication efforts. Once it is done, project managers may take steps to mitigate the risk. This includes using a communication risk assessment tool and including stakeholders in the process.
Consultation
A project's risk management requires that all stakeholders be included. There are many stakeholders to consider, including internal and external partners, as well as stakeholders that aren't directly involved in the project. To ensure that all stakeholders are fully informed about the risks and expectations, it's important to include them in the risk management process. To ensure the appropriate level of consultation, project teams should involve all stakeholders during the risk assessment and management process. Here are some suggestions to make sure that everyone is involved in the consultation process.
In addition to assessing risks, a risk management consultant will help prioritize risks. This is vital because the most high-risk areas require immediate attention. Low-risk areas will require a slower remediation plan. Consulting is a great way for organizations to identify risks and design a risk management program that meets their specific needs. Consultants will also assist with the development of an action plan that will help the organization mitigate risks and improve its overall risk management process.
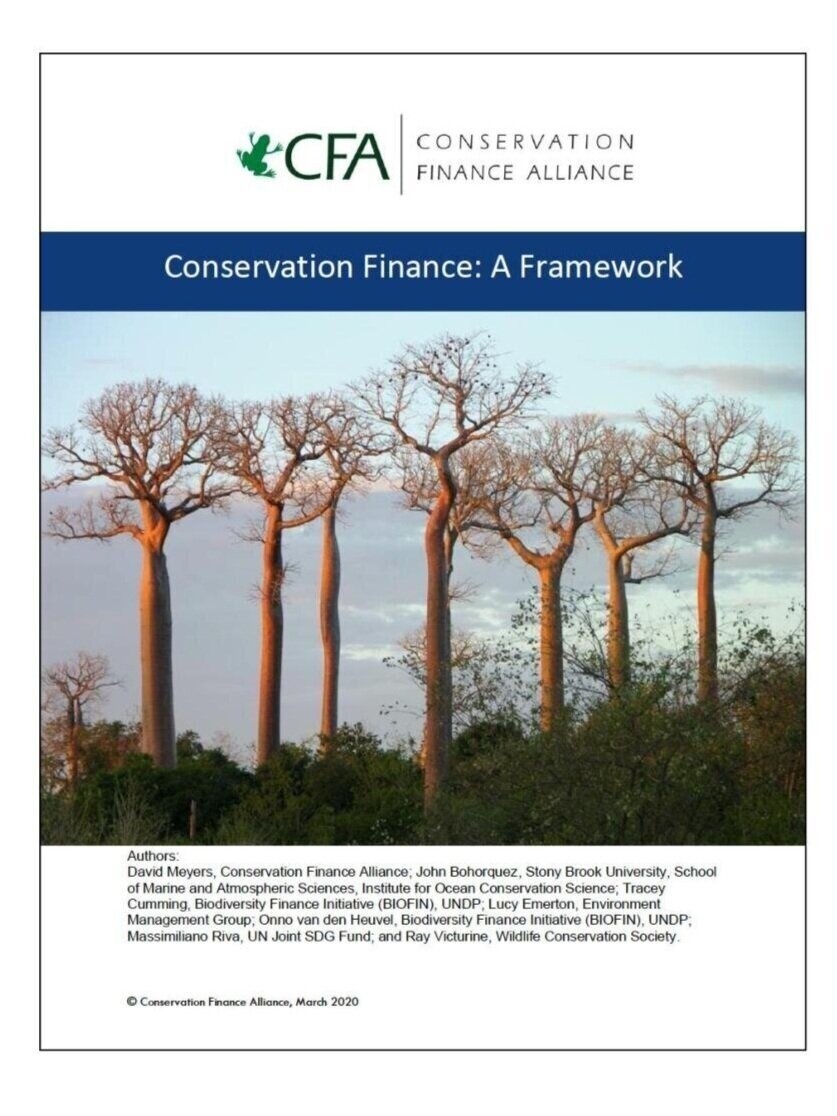
Top-down
Top-down risk management has its advantages and disadvantages. To start up it requires considerable time, effort, as well as expertise. It can be very individualized, so what one manager may have learned in one industry may not work for another. It has tremendous potential to be used as a risk management tool. It is slowly becoming more widely accepted, even though it isn't widely used. Here are some reasons why.
Top-down risk management techniques are most helpful during the initial phases of a project. These early stages are where the most benefits of risk management can be realized. The learned lessons from past projects can also be used. Additionally, top-down analysis can help to increase management accountability by using evidence-based top down risk models and techniques derived from previous projects. If implemented correctly, top-down risk management techniques can greatly reduce project risk. In addition, they can help managers and teams meet their financial obligations to stakeholders.
FAQ
What is the difference between project and program?
A project is temporary while a programme is permanent.
A project has usually a specified goal and a time limit.
This is often done by a group of people who report to one another.
A program will usually have a set number of goals and objectives.
It is usually done by one person.
How can we create a culture of success in our company?
A successful company culture is one that makes people feel valued and respected.
It's based on three main principles:
-
Everyone has something valuable to contribute
-
People are treated fairly
-
There is mutual respect between individuals and groups
These values are reflected in the way people behave. They will treat others with kindness and consideration.
They will respect the opinions of others.
They can also be a source of inspiration for others.
In addition, the company culture encourages open communication and collaboration.
People feel comfortable expressing their opinions freely without fear of reprisal.
They know that they will not be judged if they make mistakes, as long as the matter is dealt with honestly.
The company culture encourages honesty and integrity.
Everyone is aware that truth must be told.
Everyone understands that there are rules and regulations which apply to them.
People don't expect special treatment or favors.
What are the top management skills?
Any business owner needs to be able to manage people, finances, resources and time. They include the ability to manage people, finances, resources, time, and space, as well as other factors.
When you need to manage people, set goals, lead teams, motivate them, solve problems, develop policies and procedures and manage change, management skills are essential.
As you can see, there's no end to the list of managerial duties!
Statistics
- Hire the top business lawyers and save up to 60% on legal fees (upcounsel.com)
- Our program is 100% engineered for your success. (online.uc.edu)
- The average salary for financial advisors in 2021 is around $60,000 per year, with the top 10% of the profession making more than $111,000 per year. (wgu.edu)
- Your choice in Step 5 may very likely be the same or similar to the alternative you placed at the top of your list at the end of Step 4. (umassd.edu)
- The profession is expected to grow 7% by 2028, a bit faster than the national average. (wgu.edu)
External Links
How To
How can you implement the Kaizen technique?
Kaizen means continuous improvement. The Japanese philosophy emphasizes small, incremental improvements to achieve continuous improvement. This term was created by Toyota Motor Corporation in 1950. It's a team effort to continuously improve processes.
Kaizen is one of Lean Manufacturing's most efficient methods. In this concept, employees who are responsible for the production line must identify problems that exist during the manufacturing process and try to solve them before they become big issues. This improves the quality of products, while reducing the cost.
The main idea behind kaizen is to make every worker aware of what happens around him/her. It is important to correct any problems immediately if they are discovered. So, if someone notices a problem while working, he/she should report it to his/her manager.
When doing kaizen, there are some principles we must follow. The end product is always our starting point and we work toward the beginning. For example, if we want to improve our factory, we first fix the machines that produce the final product. First, we fix machines that produce components. Next, we fix machines that produce raw material. Then, we fix those who work directly with the machines.
This method is known as kaizen because it focuses upon improving every aspect of the process step by step. After we're done with the factory, it's time to go back and fix the problem.
It is important to understand how to measure the effectiveness and implementation of kaizen in your company. There are many ways you can determine if kaizen has been implemented well. One method is to inspect the finished products for defects. Another way is determining how much productivity increased after implementing kaizen.
If you want to find out if your kaizen is actually working, ask yourself why. Was it just because it was the law or because you wanted to save money? It was a way to save money or help you succeed.
Congratulations! You're now ready to get started with kaizen.