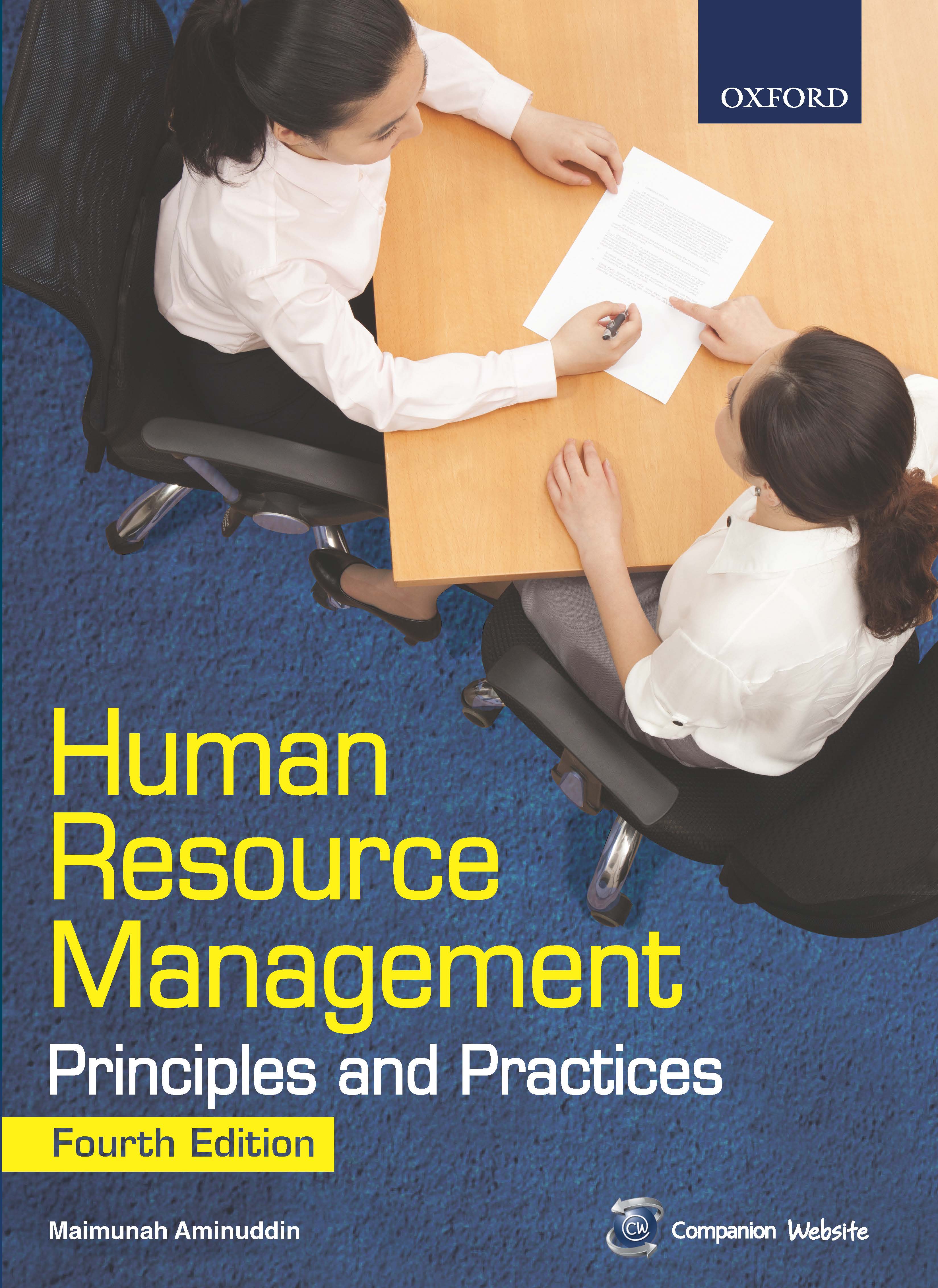
The hierarchy of control is an effective way to protect workers from hazards. It is widely accepted by many safety agencies and is commonly used in practice. It is taught to all industry managers and accepted as a standard practice. There are many variations to this system. You can find out more about the NFPA 70E hazard class system and the ARECC variant in our guide. Once you have the information you will be able apply the hierarchy better to your workplace.
NFPA 70E
NFPA 70E is a set of standards for electrical safety in the workplace. In the 2018 edition, there is an Annex Q section. This describes human performance and human errors and their potential adverse consequences. This section provides a hierarchy for controlling hazards, and prioritizes their elimination. Electrical hazards require that you eliminate any source of electricity or hazards. Personal protective equipment should only be used as a last resort.
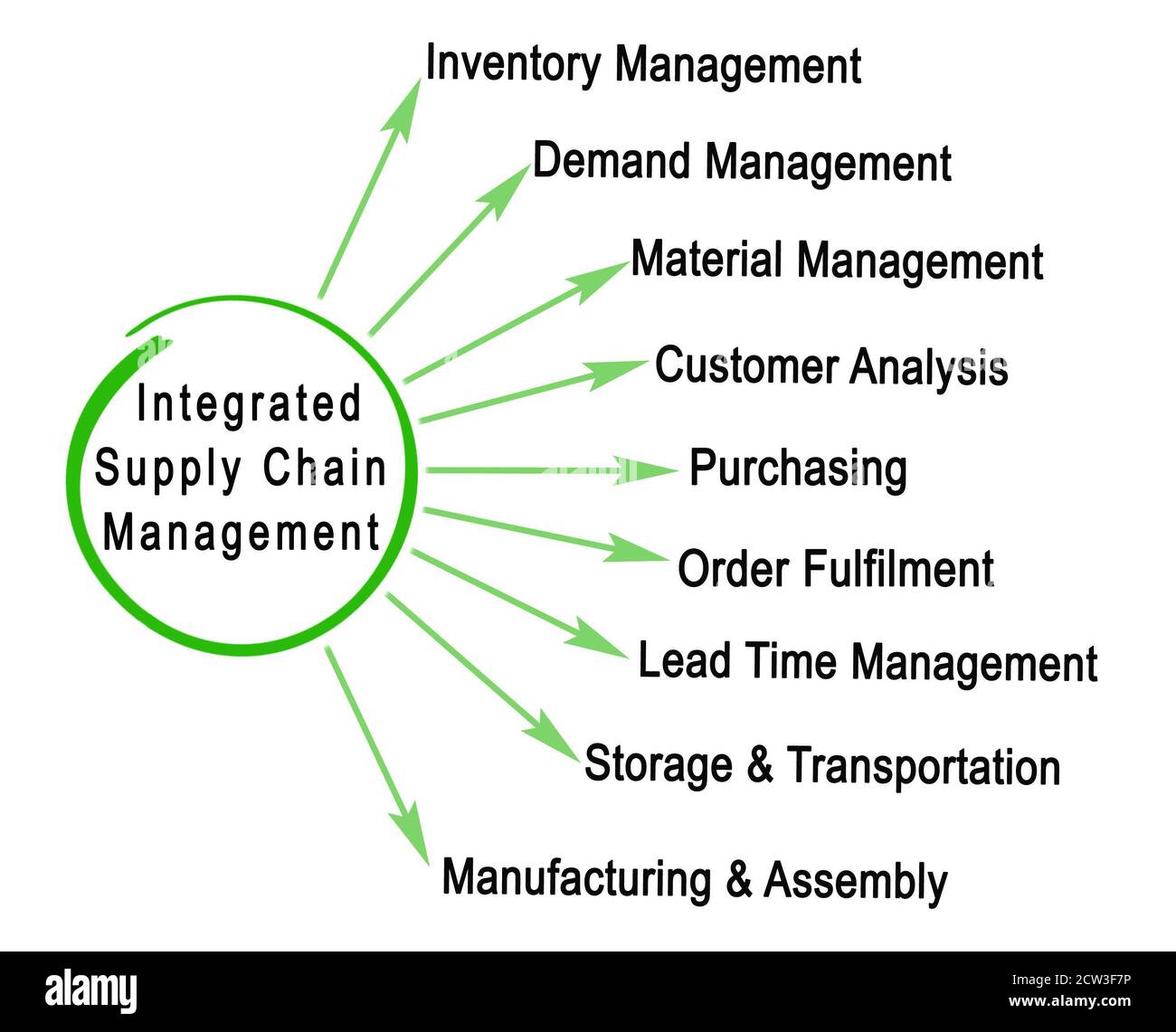
Next is to determine the degree of exposure to hazards. Then, you will need to decide on the most appropriate engineering controls that can reduce the severity. While engineering controls may reduce the danger from hazardous substances, they do not eliminate it completely. The goal of the hierarchy of control is to prevent exposure to hazards and minimize their severity. A common example is an engineering control, such as a fog machine or ventilation system, or a fire alarm.
The NFPA 70E standard also includes appendices. These documents provide information about specific procedures and practices and guidance on how to follow them. Appendices contain sample forms, PPE guidance and design requirements as well as risk assessment guidelines. Annexes can be used to guide you in implementing the standard, just like the main text. Sometimes, annexes may be used to provide additional information that can help ensure safety in a workplace or building.
Variation of ARECC
The ARECC variation is a way to reduce exposure to a particular hazard. This system is traditionally used in the United States and Canada, but it has been adapted in other countries. One example is that some countries prioritize isolation over engineering controls while others combine both. The ARECC variations include warnings and employee training. Not all hazards can be eliminated by warnings.
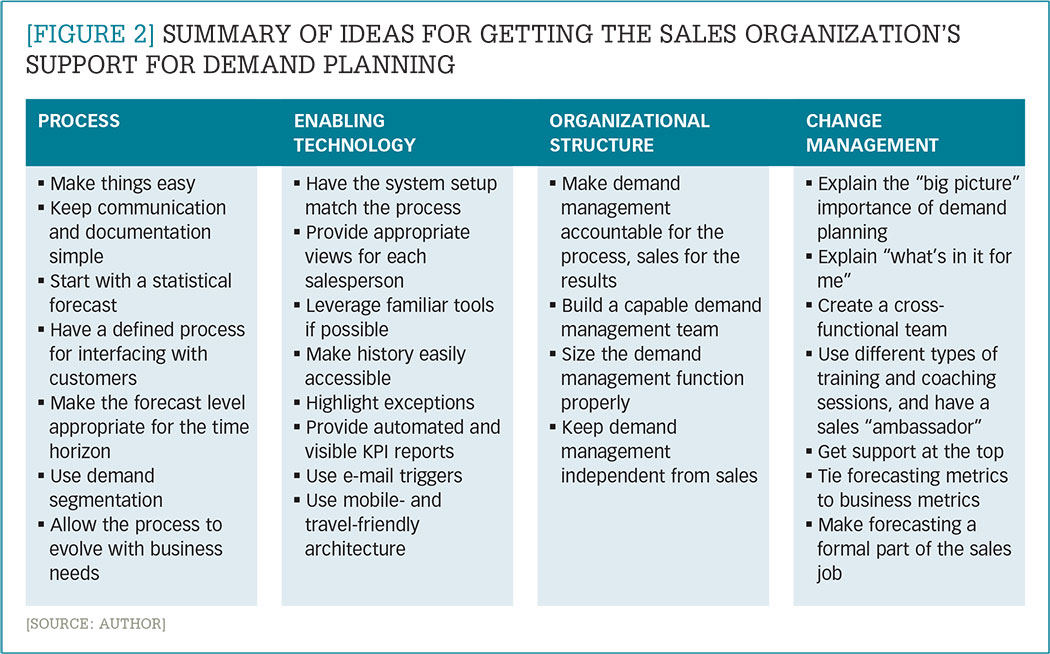
The ARECC hierarchy, or set of controls, is a framework that promotes occupational safety and health. It determines possible solutions and prioritizes them according the effectiveness. There are five categories of controls in the hierarchy: engineering controls, administrative controls, personal protective equipment, and administrative controls. Each category has specific strengths and weaknesses that are important for a particular situation. Some controls included in the ARECC hierarchy may be more effective than others.
FAQ
Which kind of people use Six Sigma
Six Sigma is well-known to those who have worked in operations research and statistics. Anybody involved in any aspect or business can benefit.
It is a commitment-intensive task that requires strong leadership skills.
What are the main four functions of management
Management is responsible to plan, organize, direct, and control people and resources. It also includes developing policies and procedures and setting goals.
Management helps an organization achieve its objectives by providing direction, coordination, control, leadership, motivation, supervision, training, and evaluation.
Management has four primary functions:
Planning - Planning involves determining what needs to be done.
Organizing – Organizing means deciding how to organize things.
Directing - Directing is when you get people to do what you ask.
Controlling - Controlling means ensuring that people carry out tasks according to plan.
How can we make our company culture successful?
Successful company culture is one where people feel valued and respected.
It is founded on three basic principles:
-
Everybody has something of value to share
-
People are treated with respect
-
People and groups should respect each other.
These values are reflected by the way people behave. They will treat others with respect and kindness.
They will be respectful of the opinions of other people.
They will also encourage others to share their ideas and feelings.
A company culture encourages collaboration and communication.
People feel free to express their views openly without fear of reprisal.
They understand that errors will be tolerated as long they are corrected honestly.
Finally, the company culture promotes integrity and honesty.
Everyone is aware that truth must be told.
Everyone knows that there are rules and regulations that apply to them.
People don't expect special treatment or favors.
What do we mean when we say "project management"?
We mean managing the activities involved in carrying out a project.
We include defining the scope of the project, identifying the requirements, preparing the budget, organizing the project team, scheduling the work, monitoring progress, evaluating results, and closing down the project.
What are the three basic management styles?
The three major management styles are authoritarian (left-faire), participative and laissez -faire. Each style has its advantages and disadvantages. Which style do YOU prefer? Why?
Autoritarian – The leader sets the direction for everyone and expects them to follow. This style works well if an organization is large and stable.
Laissez faire - Each individual can decide for himself/herself. This style works best when the organization is small and dynamic.
Participative: The leader listens to everyone's ideas and suggestions. This approach works best in small organizations where everyone feels valued.
What is the difference of leadership and management?
Leadership is about influence. Management is about controlling others.
A leader inspires followers while a manager directs workers.
A leader inspires others to succeed, while a manager helps workers stay on task.
A leader develops people; a manager manages people.
What role does a manager play in a company?
Managers' roles vary from industry to industry.
A manager is generally responsible for overseeing the day to day operations of a company.
He/she is responsible for ensuring that the company meets all its financial obligations and produces the goods or services customers want.
He/she will ensure that employees follow all rules and regulations, and adhere to quality standards.
He/she plans and oversees marketing campaigns.
Statistics
- Our program is 100% engineered for your success. (online.uc.edu)
- Your choice in Step 5 may very likely be the same or similar to the alternative you placed at the top of your list at the end of Step 4. (umassd.edu)
- As of 2020, personal bankers or tellers make an average of $32,620 per year, according to the BLS. (wgu.edu)
- This field is expected to grow about 7% by 2028, a bit faster than the national average for job growth. (wgu.edu)
- The BLS says that financial services jobs like banking are expected to grow 4% by 2030, about as fast as the national average. (wgu.edu)
External Links
How To
How can you implement the Kaizen technique?
Kaizen means continuous improvement. Kaizen is a Japanese concept that encourages constant improvement by small incremental changes. It's a team effort to continuously improve processes.
Kaizen is one of the most effective methods used in Lean Manufacturing. Employees responsible for the production line should identify potential problems in the manufacturing process and work together to resolve them. This is how you can improve the quality and lower the cost.
Kaizen is about making everyone aware of the world around them. Correct any errors immediately to avoid future problems. Report any problem you see at work to your manager.
Kaizen is based on a few principles. Start with the end product, and then move to the beginning. In order to improve our factory's production, we must first fix the machines producing the final product. Next, we repair the machines that make components. Then, the machines that make raw materials. Then we fix the workers, who directly work with these machines.
This is known as "kaizen", because it emphasizes improving each step. Once we have finished fixing the factory, we return to the beginning and work until perfection.
It is important to understand how to measure the effectiveness and implementation of kaizen in your company. There are several ways to determine whether kaizen is working well. One method is to inspect the finished products for defects. Another way is to check how much productivity has grown since kaizen was implemented.
You can also find out if kaizen works by asking yourself why you decided to implement it. Did you do it because it was legal or to save money? It was a way to save money or help you succeed.
If you answered yes to any one of these questions, congratulations! You're now ready to get started with kaizen.